Agregat chłodniczy jest agregatem chłodniczym składającym się z zamkniętego obiegu czynnika chłodniczego (w tym sprężarki, skraplacza, zaworu termostatycznego, parownika, filtra osuszacza, rur łączących oraz zestawu elementów sterujących i sterujących) oraz obwodu wodnego (w tym zawory kulowe, parownik, zbiornik akumulacyjny oraz pompę wodną) podłączoną do rurociągów, które zapewniają transport wody od odbiorców iz powrotem. Parownik jest wspólnym elementem dla obu obwodów. Po przejściu przez parownik woda ochładza się (podczas pracy sprężarki).
Temperatura wrzenia
Temperatura wrzenia cieczy zależy od ciśnienia otoczenia. Im niższe jest to ciśnienie, tym niższa jest temperatura wrzenia. Na przykład dobrze wiadomo, że woda wrze w temperaturze 100 ° C. Ale dzieje się tak tylko przy normalnym ciśnieniu atmosferycznym (760 mmHg). Wraz ze wzrostem ciśnienia temperatura wrzenia wzrośnie, a wraz ze spadkiem (na przykład wysoko w górach) woda zagotuje się w temperaturze znacznie niższej niż 100 ° C. Średnio, gdy ciśnienie zmienia się o 27 mm Hg. Art. temperatura wrzenia zmieni się o 1 ° C.
Różne płyny gotują się w różnych temperaturach nawet przy tym samym ciśnieniu zewnętrznym. Na przykład ciekły azot wrze w temperaturze bliskiej -77 ° C, a freon R-22 stosowany w technologii chłodniczej wrze w temperaturze -40,8 ° C (przy normalnym ciśnieniu atmosferycznym).
Ciepło parowania
Kiedy ciecz paruje, ciepło jest absorbowane z otoczenia. Przeciwnie, gdy para się skrapla, uwalniane jest ciepło. Ciepło parowania cieczy jest bardzo wysokie. Na przykład energia potrzebna do odparowania 1 g wody o temperaturze 100 ° C (539 kalorii / g) to znacznie więcej niż energia potrzebna do podgrzania tej wody od 0 ° C do 100 ° C (100 kalorii / g)! Jeśli ciekły freon zostanie umieszczony w otwartym naczyniu (o ciśnieniu atmosferycznym i temperaturze pokojowej), natychmiast się zagotuje, pochłaniając dużą ilość ciepła z otoczenia. Zjawisko to stosuje się w maszynie chłodniczej. Tylko w nim freon zamienia się w parę w specjalnym przedziale - parowniku. Rurki parownika są wdmuchiwane przez strumień powietrza. Wrzący freon pochłania ciepło z tego strumienia powietrza, chłodząc je. Ale w maszynie chłodniczej niemożliwe jest jedynie odparowanie freonu, pochłaniającego ciepło. W końcu powstanie w nim duża liczba par i konieczne będzie ciągłe dostarczanie coraz większej ilości płynnego freonu. Dlatego w maszynie chłodniczej odbywa się również odwrotny proces kondensacji - konwersja pary wodnej na ciecz. Kondensacja dowolnej cieczy wytwarza ciepło, które następnie przedostaje się do środowiska. Temperatura skraplania, podobnie jak temperatura wrzenia, zależy od ciśnienia zewnętrznego. Przy podwyższonym ciśnieniu kondensacja może wystąpić w bardzo wysokich temperaturach. Na przykład freon R-22 zaczyna kondensować w temperaturze + 55 ° C, jeśli znajduje się pod ciśnieniem 23 atmosfer (około 17,5 tys. MmHg).
Maszyna chłodnicza
W maszynie chłodniczej freon kondensuje w specjalnej komorze - skraplaczu. Ciepło uwalniane podczas kondensacji jest usuwane przez przepływ płynu chłodzącego lub powietrza. Ponieważ maszyna chłodnicza musi działać w sposób ciągły, ciekły freon musi stale wpływać do parownika, a jego para do skraplacza. Proces ten jest cykliczny, ograniczona ilość freonu krąży w maszynie chłodniczej, odparowując i kondensując.
Jednym z głównych elementów agregatu jest skraplacz, który służy do przenoszenia energii cieplnej z czynnika chłodniczego do środowiska. Najczęściej ciepło jest przekazywane do wody lub powietrza. Ciepło generowane w skraplaczu jest około 30% wyższe niż wydajność chłodnicza agregatu. Na przykład, jeśli wydajność chłodnicza maszyny wynosi 20 kW, wówczas skraplacz wytwarza 25–27 kW ciepła.
Cykl chłodzenia sprężarkowego składa się z czterech głównych elementów:
1. kompresor
2. parownik
3. kondensator
4. regulator przepływu.
Te główne elementy są połączone rurociągami w system zamkniętygdzie krąży czynnik chłodniczy (zwykle freon). Czynnik chłodniczy krąży w obwodzie przez sprężarkę agregatu chłodniczego.
Cykl chłodzenia kompresyjnego
Na wylocie z parownika czynnikiem chłodniczym jest para o niskiej temperaturze i niskim ciśnieniu. Następnie sprężarka absorbuje czynnik chłodniczy, ciśnienie wzrasta do około 20 atm., A temperatura osiąga 70 - 90 ° C. Następnie gorąca para czynnika chłodniczego dostaje się do skraplacza, gdzie jest chłodzona i skraplana. Do chłodzenia używa się wody lub powietrza. Na wylocie skraplacza czynnik chłodniczy jest cieczą pod wysokim ciśnieniem. Wewnątrz skraplacza para musi całkowicie przejść do stanu ciekłego. W tym celu temperatura cieczy opuszczającej skraplacz jest o kilka stopni (zwykle 4-6 ° C) niższa niż temperatura kondensacji przy danym ciśnieniu. Następnie czynnik chłodniczy (mający w tej chwili stan skupienia cieczy pod wysokim ciśnieniem i temperaturą) wchodzi do regulatora przepływu. Tutaj ciśnienie gwałtownie spada i dochodzi do częściowego parowania.
Mieszanina pary i cieczy wchodzi do wlotu parownika. W parowniku ciecz musi całkowicie przejść do stanu pary. Dlatego temperatura pary na wylocie z parownika jest nieco wyższa niż temperatura wrzenia przy danym ciśnieniu (zwykle 5-8 ° C). Jest to konieczne, aby nawet małe kropelki ciekłego czynnika chłodniczego nie dostały się do sprężarki, w przeciwnym razie sprężarka może zostać uszkodzona. Przegrzana para wodna powstająca w parowniku opuszcza go i cykl wznawia się jako pierwszy.
Tak więc ograniczona ilość czynnika chłodniczego stale krąży w maszynie chłodniczej, zmieniając stan agregacji z okresowo zmieniającą się temperaturą i ciśnieniem.
Każdy cykl ma dwa zdefiniowane poziomy ciśnienia. Po stronie wysokiego ciśnienia znajduje się kondensat czynnika chłodniczego i skraplacz. Po stronie niskiego ciśnienia znajduje się parownik, a ciekły czynnik chłodniczy przekształca się w parę. Granica między obszarami wysokiego i niskiego ciśnienia przebiega w dwóch punktach - na wylocie sprężarki (zawór wylotowy) i na wylocie regulatora przepływu.
Entalpia czynnika chłodniczego
Cykl chłodzenia zachodzący w agregacie jest dogodnie przedstawiony graficznie. Wykres pokazuje stosunek ciśnienia i zawartości ciepła (entalpii) czynnika chłodniczego. Entalpia jest funkcją stanu, której przyrost w procesie ze stałym ciśnieniem jest równy ciepłu odbieranemu przez system.
- Lewa gałąź krzywej odpowiada nasyconemu płynowi
- Prawa strona odpowiada parze nasyconej.
- W punkcie krytycznym gałęzie krzywej są połączone, a substancja może znajdować się zarówno w stanie ciekłym, jak i gazowym.
- Wewnątrz krzywej znajduje się strefa odpowiadająca mieszaninie pary i cieczy.
- Na lewo od krzywej (w obszarze niższej entalpii) znajduje się przechłodzona ciecz.
- Po prawej stronie krzywej (w obszarze o większej entalpii) jest para przegrzana.
Teoretyczny cykl chłodzenia
W sprężarce
Zimno nasycone pary czynnika chłodniczego przedostają się do sprężarki agregatu chłodniczego (punkt C1). Podczas ściskania wzrasta jego ciśnienie i temperatura (punkt D). Entalpia również wzrasta o kwotę równą rzutowi linii C1-D. Na schemacie jest to segment НС1-НD.
Kondensacja
Pod koniec cyklu sprężania czynnika chłodniczego gorąca para dostaje się do skraplacza. Tutaj, przy stałej temperaturze i ciśnieniu, dochodzi do kondensacji, a gorąca para zamienia się w gorącą ciecz. Chociaż temperatura jest prawie stała, entalpia zmniejsza się podczas przejścia fazowego, a uwalniane ciepło jest usuwane ze skraplacza. Proces ten jest wyświetlany na schemacie w postaci segmentu równoległego do osi poziomej (ciśnienie jest stałe).
Proces w skraplaczu agregatu chłodniczego odbywa się w trzech etapach: usunięcie przegrzania (D-E), kondensacja (E-A) i przechłodzenie cieczy (A-A1). Wykres na schemacie D-A1 odpowiada zmianie entalpii czynnika chłodniczego w skraplaczu i pokazuje, ile ciepła jest uwalniane podczas tego procesu.
Usuwanie przegrzania.
W tym procesie temperatura pary spada do temperatury nasycenia. Nadmiar ciepła jest usuwany, ale zmiana stanu agregacji nie występuje. Na tym etapie usuwa się około 10 do 20% ciepła.Kondensacja
Na tym etapie zmienia się stan zagregowanego czynnika chłodniczego. Temperatura pozostaje stała. Na tym etapie około 60–80% ciepła jest usuwane.Przechłodzenie cieczy
W tym procesie ciekły czynnik chłodniczy jest schładzany i uzyskuje się przechłodzoną ciecz. Stan agregacji nie zmienia się. Na tym etapie dochładzanie cieczy poprawia wydajność urządzenia chłodniczego. Przy stałym poziomie zużycia energii obniżenie temperatury o 1 stopień zwiększa wydajność agregatu o 1%.Regulator przepływu
Przechłodzona ciecz o parametrach punktu A2 wchodzi do regulatora agregatu chłodniczego. Jest to kapilara lub termostatyczny zawór rozprężny. Gwałtowny spadek ciśnienia występuje w regulatorze. Bezpośrednio po regulatorze czynnik chłodniczy zaczyna wrzeć. Parametry powstałej mieszaniny pary i cieczy odpowiadają punktowi B.W parowniku
Mieszanina pary i cieczy (punkt B) dostaje się do parownika urządzenia chłodniczego, gdzie pochłania ciepło z otoczenia i całkowicie przenosi się do pary (punkt C1). Proces ten zachodzi w stałej temperaturze, ale entalpia wzrasta. Na wyjściu z parownika parowy czynnik chłodniczy nieco się przegrzewa (segment C1-C2), przez co krople cieczy całkowicie odparowują. Aby to zrobić, konieczne jest zwiększenie powierzchni powierzchni wymiany ciepła parownika (o 4-6% dla każdego stopnia przegrzania). Zwykle przegrzanie wynosi 5-8 stopni, a wzrost powierzchni wymiany ciepła sięga 20%. W parowniku agregatu entalpia czynnika chłodniczego zmienia się o wartość HB-HC2, równą rzutowi krzywej parowania na osi poziomej.Prawdziwy cykl chłodzenia
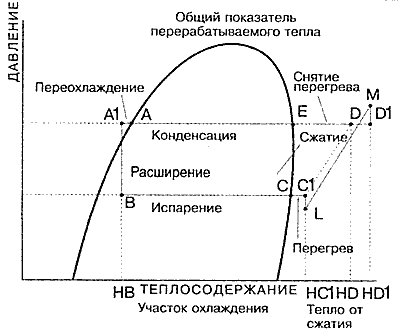
Rzeczywisty cykl chłodzenia różni się od ideału. Jest to spowodowane stratami ciśnienia występującymi na przewodach ssawnym i tłocznym urządzenia chłodniczego, a także w zaworach sprężarki. Dlatego wyświetlanie rzeczywistego cyklu na schemacie zależności między ciśnieniem a entalpią jest nieco inne.
Ze względu na straty ciśnienia na wlocie do sprężarki ssanie musi odbywać się przy ciśnieniu niższym niż ciśnienie parowania (segment C1-L). Ponadto ze względu na straty ciśnienia na wylocie sprężarka musi sprężać pary czynnika chłodniczego do ciśnienia wyższego niż ciśnienie kondensacji (M-D1). W ten sposób zwiększa się praca kompresji. Taka kompensacja strat ciśnienia w prawdziwym agregacie chłodniczym zmniejsza wydajność cyklu.
Oprócz strat ciśnienia w rurociągu istnieją inne odchylenia od idealnego cyklu. Po pierwsze, faktyczne sprężanie czynnika chłodniczego w sprężarce nie może być ściśle adiabatyczne (bez dostarczania i odprowadzania ciepła). Dlatego praca przy kompresji jest wyższa niż obliczona teoretycznie. Po drugie, sprężarka agregatu ma mechaniczne straty energii, co prowadzi do wzrostu wymaganej mocy silnika elektrycznego.
Wydajność cyklu chłodzenia agregatu
Wyświetlanie wykresów:C1-L - strata ciśnienia ssania
M-D1 - strata ciśnienia na wylocie
HD-HC1 - teoretyczna zmiana entalpii (zawartości ciepła) podczas kompresji
HD1-HC1 - rzeczywista zmiana entalpii (zawartości ciepła) podczas kompresji
C1D - Kompresja teoretyczna
LM - prawdziwa kompresja
Aby wybrać najlepszy z cykli chłodzenia, należy ocenić ich skuteczność. Zazwyczaj wskaźnikiem wydajności cyklu maszyny chłodniczej jest wydajność lub współczynnik wydajności termicznej (termodynamicznej).
Współczynnik sprawności cieplnej- jest to: stosunek zmiany entalpii czynnika chłodniczego w parowniku (HC-HB) do zmiany entalpii podczas sprężania (HD-HC).lub: stosunek mocy chłodzenia do energii elektrycznej zużywanej przez sprężarkę agregatu chłodniczego.
Na przykład, jeśli współczynnik sprawności cieplnej urządzenia chłodniczego wynosi 2, wówczas na każdy kW zużytej energii elektrycznej urządzenie to wytwarza 2 kW chłodu.
Kondensator Zasada pracy.
Skraplacze chłodzone powietrzem
![]() 1 rura miedziana 2 żebra chłodzące |
Najczęściej stosowane są skraplacze chłodzone powietrzem. Chłodzony powietrzem skraplacz składa się z wentylatora z silnikiem elektrycznym i wymiennika ciepła. Czynnik chłodniczy przepływa przez rury, a wentylator przepuszcza powietrze przez rury. Zazwyczaj prędkość przepływu wynosi 1 - 3,5 m / s. Najczęściej wymiennik ciepła składa się z żebrowanych rur miedzianych o średnicy 6 - 20 mm z odległością między żebrami 1-3 mm. Miedź jest używana, ponieważ jest łatwa w obróbce, nie utlenia się i ma wysoką przewodność cieplną. Płetwy są zwykle wykonane z aluminium. Wybór średnicy rury zależy od wielu czynników: straty ciśnienia, łatwości obróbki itp. Rodzaj żeber może być różny i znacząco wpływa na parametry termiczne i hydrauliczne wymiennika ciepła jako całości. Na przykład złożony profil żeber z licznymi występami i rowkami powoduje turbulencję (turbulencję) powietrza przemywającego wymiennik ciepła. W rezultacie zwiększa się efektywność wymiany ciepła z czynnika chłodniczego do powietrza i wzrasta wydajność chłodnicza agregatu chłodniczego. |
Stosowane są dwa rodzaje połączeń rur z żebrami:
Otwory w żebrach, w których rury wymiennika ciepła są bezpośrednio włożone. Ta metoda jest prostsza, ale zmniejsza przenoszenie ciepła z powodu nieszczelnego styku. Ponadto korozja może pojawić się w zanieczyszczonym środowisku wzdłuż konturu, co dodatkowo zmniejsza wydajność wymiany ciepła.
Kołnierze (kołnierze) w miejscach połączenia rur wymiennika ciepła. Ta metoda jest droższa i bardziej skomplikowana, ale zapewnia wzrost powierzchni wymiany ciepła.
Ponadto przenoszenie ciepła przez czynnik chłodniczy jest zwiększane przez pofałdowanie wewnętrznej powierzchni rur wymiennika ciepła. Powoduje to turbulencje w przepływie czynnika chłodniczego.
Zwykle skraplacz ma od jednego do czterech rzędów rur usytuowanych w kierunku przepływu czynnika chłodniczego. Często rury są ułożone naprzemiennie w celu zwiększenia wydajności wymiany ciepła.
Szybkość wymiany ciepła zmienia się podczas ruchu czynnika chłodniczego przez rury. Gorący czynnik chłodniczy dostaje się do wymiennika z góry i przesuwa się w dół.
Na początkowym etapie (5% powierzchni) chłodzenie jest najbardziej intensywne, ponieważ maksymalna różnica temperatur między czynnikiem chłodniczym a powietrzem chłodzącym oraz duża prędkość przepływu czynnika chłodniczego.
Główna sekcja wymiennika ciepła stanowi około 85% powierzchni. W tym obszarze czynnik chłodniczy skrapla się w stałej temperaturze.
Pozostałe 10% powierzchni wymiennika ciepła służy do dodatkowego chłodzenia ciekłego czynnika chłodniczego.
Temperatura kondensacji czynnika chłodniczego (freonu) jest o 10 do 20 stopni wyższa niż temperatura otoczenia i zwykle wynosi 42-55 ° C. Ogrzane powietrze opuszczające wymiennik ciepła jest tylko o 3-5 stopni zimniejsze od temperatury kondensacji.
Skraplacze chłodzone wodą
Istnieją trzy rodzaje skraplaczy chłodzonych wodą:- Shell and tube
- Wpisz „rura w rurze”
- Lamellar.
Kondensatory płaszczowe i lampowe
W procesie wymiany ciepła nie bierze udziału całe powietrze dostarczane do parownika, ponieważ jego część przechodzi wzdłuż obrzeża obok wymiennika ciepła. Procent powietrza, które przechodzi przez parownik i zachowuje swoje parametry, nazywa się współczynnikiem przecieku. Powinien dążyć do obniżenia współczynnika wycieku powietrza.
Skraplacz typu rura w rurze to układ dwóch rur spiralnych, jedna umieszczona wewnątrz drugiej. Czynnik chłodniczy przepływa przez jedną z rur (zewnętrzną lub wewnętrzną), a woda przemieszcza się wzdłuż drugiej. Rura wewnętrzna jest wykonana z miedzi, a zewnętrzna z miedzi lub stali. Powierzchnia rurek może mieć żebra, co zwiększa efektywność wymiany ciepła. Ciecze poruszają się w nadciągających przepływach, woda wpada z dołu i płynie z góry, a czynnik chłodniczy - i na odwrót. Skraplacze rurowe są stosowane w samodzielnych urządzeniach klimatyzacyjnych i urządzeniach chłodniczych małej mocy. Wadą tego typu kondensatorów jest to, że konstrukcja jest jednoczęściowa i możliwe jest jedynie chemiczne czyszczenie rurki.Kondensatory płytowe
Kondensatory płytowe składają się z rzędów płyt stalowych ułożonych „w jodełkę”. W wymienniku ciepła czynnik chłodniczy i woda przemieszczają się ku sobie wzdłuż niezależnych obwodów cyrkulacyjnych.
Dlatego są szeroko stosowane w lodówkach małej i średniej mocy.
Jeśli temperatura wody na wlocie do skraplacza wynosi 16 stopni, to temperatura kondensacji wynosi 32-36 stopni. Przy temperaturze wody + 24 ° C czynnik chłodniczy skrapla się w 38-40 ° C.
Maksymalne dopuszczalne ciśnienie w trybie roboczym od strony obwodu chłodniczego wynosi 2,45 MPa, a od strony obwodu wodnego - 1 MPa.
Parownik
Jednym z głównych elementów agregatu jest parownik, który służy do chłodzenia środowiska pracy. Jako medium robocze agregatu chłodniczego stosuje się powietrze, wodę lub płyny zawierające płyn niezamarzający. Różne typy parowników przeznaczone są do chłodzenia różnych rodzajów mediów roboczych:- Shell and tube
- Lamellar
Parowniki płaszczowo-rurowe
Parownik płaszczowo-rurowy jest stalowym cylindrem, stalowe kratownice są zainstalowane na obu końcach cylindra, do których zamontowane są głowice z dyszami do podłączenia do wodnego układu chłodzenia. Rurki miedziane, przez które przepływa woda, są wtłaczane do tych siatek. Rury są najczęściej wykonane z miedzi i mają średnicę 20 mm i 25 mm. Na zewnątrz są żebrowane w celu zwiększenia wymiany ciepła.
Czynnik chłodniczy krąży w rurach, wydostając się z dna parownika i stopniowo podnosząc się przez rury. Na zewnątrz rury są myte wodą, która jest chłodzona podczas wymiany ciepła z zimnym czynnikiem chłodniczym.
Woda w parowniku płaszczowo-rurowym krąży prostopadle do rur i ma prędkość od 0,5 do 3 m / s ze względu na ścianki działowe znajdujące się wewnątrz obudowy parownika.
Parowniki płaszczowo-rurowe nadają się do przenoszenia różnych czynników chłodniczych. Moc tych parowników waha się od 7 do 200-250 kW.
Parowniki płytowe
Parowniki płytowe składają się z rzędów stalowych płyt ułożonych „w jodełkę”. W wymienniku ciepła czynnik chłodniczy i woda przemieszczają się ku sobie wzdłuż niezależnych obwodów cyrkulacyjnych.Zalety:
- bardzo wysoka wydajność wymiany ciepła.
- zwartość i lekkość.
- bardziej odporny na zamarzanie w przypadku awarii niż inne rodzaje parowników.
Parowniki do chłodzenia powietrzem
Parowniki powietrza są wymiennikami ciepła z jednym lub więcej (4-6) rzędami rurek. Czynnik chłodniczy przepływa wewnątrz rur, a chłodzone powietrze przepływa między żebrami parownika (na zewnątrz rur).
Najczęściej parownik do chłodzenia powietrza składa się z żebrowanych rur miedzianych o średnicy 8–13 mm (5/16 ”, 3/8” i 1/2 ”) o odległości między żebrami 1,4–1,8 mm. Miedź jest używana, ponieważ jest łatwa w obróbce, nie utlenia się i ma wysoką przewodność cieplną, a żebra są zwykle wykonane z aluminium.
Jeśli wydajność agregatu chłodniczego jest wystarczająco duża, wówczas parowniki powietrza są wykonane z dwoma lub więcej obiegami chłodzenia. Każdy obwód ma niezależne źródło czynnika chłodniczego poprzez dystrybutor podłączony do niego cienkimi rurkami. Wszystkie obwody są wypełnione równą ilością czynnika chłodniczego. Przepływ powietrza jest równomiernie rozłożony na wymienniku ciepła, z wyłączeniem oblodzenia poszczególnych sekcji parownika.
Aby osiągnąć najlepszą jakość i stabilność parownika agregatu, moc powinna wynosić 3-7 kW dla każdego obwodu wymiany ciepła (przy zastosowaniu najczęściej stosowanego czynnika chłodniczego R-22).
Rozmiar parownika zależy od objętości schłodzonego powietrza. Objętość powietrza wynosi około 195 metrów sześciennych / godzinę na każdy kW wydajności chłodniczej instalacji. Całkowita wydajność chłodnicza parownika zależy od temperatury parowania czynnika chłodniczego (stała, ustalona podczas projektowania urządzenia chłodniczego) oraz temperatury powietrza dolotowego (zależy od warunków pracy).
Prędkość powietrza wchodzącego do parownika wynosi zwykle 2–3 m / s. Jeśli prędkość jest wyższa, krople kondensatu mogą ślizgać się na wylocie z wymiennika ciepła. W parowniku, podobnie jak w innych elementach agregatu, występują straty ciśnienia. Zależą one od średnicy rur parownika, konfiguracji żeber, prędkości powietrza i ilości kondensatu na żebrach.
Wskaźnik wycieku (bypass)
Korzyści z niskiego wskaźnika wycieków:
- Zwiększa temperaturę parowania i wydajność agregatu
- Możliwe jest zmniejszenie wielkości sprężarki
- Możesz ograniczyć się do mniejszej powierzchni wymiennika ciepła. Potrzebne jest mniej rur wymiennika ciepła.
Kompresor
Jednym z głównych elementów każdego agregatu chłodniczego jest kompresor.
Sprężarka absorbuje opary czynnika chłodniczego o niskiej temperaturze i ciśnieniu, a następnie ściska je, podwyższając temperaturę (do 70 - 90 ° C) i ciśnienie (do 15 - 25 atm), a następnie kieruje opary czynnika chłodniczego do skraplacza.
Głównymi cechami sprężarki są stopień sprężania (sprężanie) i ilość czynnika chłodniczego, który może pompować. Współczynnik sprężania jest stosunkiem maksymalnego ciśnienia wylotowego pary czynnika chłodniczego do maksymalnego wlotu.
Lodówki używają dwóch rodzajów sprężarek:
Tłok - z tłokami tłokowymi w cylindrach
Obrotowy, śrubowy i spiralny - z obrotowym ruchem części roboczych
1. Sprężarki tłokowe
2. Sprężarki rotacyjne
3. Sprężarki spiralne SCROLL
4. Sprężarki śrubowe
Sprężarki tłokowe
Gdy tłok (3) przesuwa się w górę cylindra sprężarki (4), czynnik chłodniczy jest sprężany. Tłok jest poruszany silnikiem elektrycznym przez wał korbowy (6) i korbowód (5).
Pod wpływem ciśnienia pary zawory ssące i wydechowe sprężarki agregatu chłodniczego otwierają się i zamykają.
Rysunek 1 pokazuje fazę absorpcji czynnika chłodniczego do sprężarki. Tłok zaczyna opadać z górnego punktu, podczas gdy w komorze sprężarki powstaje próżnia i otwiera się zawór wlotowy (12). Czynnik chłodniczy o niskiej temperaturze i niskim ciśnieniu dostaje się do przestrzeni roboczej sprężarki.
Ryc. 2 pokazuje fazę sprężania pary i jej wylot ze sprężarki. Tłok unosi się i spręża parę. Jednocześnie otwiera się zawór wylotowy sprężarki (1) i para pod wysokim ciśnieniem opuszcza sprężarkę.
Główne modyfikacje sprężarek tłokowych (różnią się konstrukcją, typem silnika i przeznaczeniem):
- Sprężarki hermetyczne
- Sprężarki półhermetyczne
- Otwórz sprężarki
Sprężarki hermetyczne
Stosowany w agregatach chłodniczych małej mocy (1,5 - 35 kW). Silnik elektryczny znajduje się w szczelnej obudowie sprężarki. Silnik jest chłodzony przez sam czynnik ssący.Sprężarki półhermetyczne
Stosowany w średnich agregatach chłodniczych (30 - 300 kW). W sprężarkach półhermetycznych silnik elektryczny i sprężarka są połączone bezpośrednio i umieszczone w jednym składanym pojemniku. Zaletą tego rodzaju sprężarki jest to, że w przypadku uszkodzenia silnik można usunąć w celu naprawy zaworów, tłoka i innych części sprężarki. Silnik jest chłodzony przez sam czynnik ssący.Otwórz sprężarki
Mają zewnętrzny silnik elektryczny, wyjęty na zewnątrz obudowy i podłączony bezpośrednio do sprężarki lub przez przekładnię. Moc wielu agregatów chłodniczych może być regulowana w sposób ciągły za pomocą falowników - specjalnych urządzeń, które zmieniają prędkość obrotową sprężarki. W sprężarkach półhermetycznych możliwy jest także inny sposób regulacji mocy - obejście pary z wyjścia do wejścia lub zamknięcie części zaworów ssących.Główne wady sprężarek tłokowych:
Fale ciśnienia pary czynnika chłodniczego na wylocie, powodujące wysoki poziom hałasu.Wysokie obciążenia rozruchowe, wymagające dużej rezerwy mocy i prowadzące do zużycia sprężarki.
Sprężarki rotacyjne
Zasada działania rotacyjnych sprężarek rotacyjnych opiera się na absorpcji i sprężaniu gazu podczas rotacji płyt.Ich zaletą w stosunku do sprężarek tłokowych są pulsacje przy niskim ciśnieniu i spadek prądu przy rozruchu.
Istnieją dwie modyfikacje sprężarek rotacyjnych:
- Z nieruchomymi płytkami
- Z obrotowymi płytkami
Naprawiono sprężarkę płytową
W sprężarce ze stacjonarnymi płytami czynnik chłodniczy jest sprężany za pomocą mimośrodu zamontowanego na wirniku silnika. Gdy wirnik obraca się, mimośrod toczy się wzdłuż wewnętrznej powierzchni cylindra sprężarki, a pary czynnika chłodniczego przed nim są sprężane, a następnie wypychane przez zawór wylotowy sprężarki. Płytki oddzielają obszary wysokiego i niskiego ciśnienia pary czynnika chłodniczego wewnątrz cylindra sprężarki.
Kompresja i odsysanie trwa
Kompresja jest zakończona, para ostatecznie wypełniła przestrzeń wewnątrz cylindra sprężarki.
Sprężarka rotacyjna
Steam wypełnia dostępną przestrzeń
Rozpoczyna się sprężanie pary wodnej w sprężarce i pochłanianie nowej porcji czynnika chłodniczego
Kompresja i odsysanie są zakończone.
Rozpoczyna się nowy cykl ssania i kompresji.
Sprężarki spiralne SCROLL
Sprężarki spiralne są stosowane w lodówkach małej i średniej mocy.
Taki kompresor składa się z dwóch stalowych spiral. Są one wkładane jedna w drugą i rozszerzają się od środka do krawędzi cylindra sprężarki. Wewnętrzna spirala jest nieruchoma, a zewnętrzna obraca się wokół niej.
Spirale mają specjalny profil (ewolwentowy), który pozwala im się toczyć bez poślizgu. Zwój sprężarki jest zamontowany na mimośrodie i toczy się po wewnętrznej powierzchni innego zwoju. W takim przypadku punkt styku spirali stopniowo przesuwa się od krawędzi do środka. Para czynnika chłodniczego przed linią dotykową jest sprężana i wpychana do centralnego otworu w pokrywie sprężarki. Punkty dotykowe znajdują się na każdym zwoju wewnętrznej spirali, więc pary są ściśnięte bardziej płynnie, w mniejszych porcjach niż w innych typach sprężarek. W rezultacie obciążenie silnika sprężarki jest zmniejszone, zwłaszcza podczas uruchamiania sprężarki.
Para czynnika chłodniczego przedostaje się przez wlot cylindrycznej części obudowy, chłodzi silnik, a następnie jest sprężana pomiędzy spiralami i wychodzi przez wylot w górnej części obudowy sprężarki.
Wady sprężarek spiralnych:
- Złożoność produkcji.
- Konieczne jest bardzo dokładne dopasowanie spiral i szczelność na ich końcach.
Sprężarki śrubowe są stosowane w agregatach chłodniczych o dużej mocy (150–3500 kW). Istnieją dwie modyfikacje tego typu:
- Pojedyncza śruba
- Podwójna śruba
Sprężarka śrubowa jednoślimakowa
Modele jednośrubowe mają jedno lub dwa koła zębate satelitarne połączone z rotorem z boku.
Pary czynnika chłodniczego są sprężane za pomocą wirników obracających się w przeciwnych kierunkach. Ich obrót zapewnia centralny wirnik w postaci śruby. Para czynnika chłodniczego dostaje się przez wlot sprężarki, chłodzi silnik, a następnie wchodzi do zewnętrznego sektora obracających się kół zębatych wirników, jest sprężana i wychodzi przez zawór przesuwny do wylotu.
Śruby sprężarki muszą ściśle przylegać, dlatego stosowany jest olej smarowy. Następnie olej jest oddzielany od czynnika chłodniczego w specjalnym separatorze kompresorowym.
Sprężarka dwuśrubowa
Modele z podwójną śrubą wyróżniają się zastosowaniem dwóch wirników - głównego i napędu.
Sprężarki śrubowe nie mają zaworów wlotowych i wylotowych. Czynnik chłodniczy jest stale zasysany z jednej strony sprężarki, a zrzut z drugiej strony. W tej metodzie sprężania poziom hałasu jest znacznie niższy niż w sprężarkach tłokowych.
Sprężarki śrubowe umożliwiają płynną regulację mocy agregatu poprzez zmianę prędkości obrotowej silnika.
Regulator przepływu
1. Rurka kapilarna2. Termostatyczny zawór rozprężny
Kapilara
Płynny czynnik chłodniczy przepływający ze skraplacza do parownika musi zostać dozowany. Jest to realizowane za pomocą regulatora przepływu.
Najprostszą wersją regulatora jest kapilara o średnicy około 1 mm. Są one stosowane w klimatyzatorach układów split o niskiej mocy.
Zalety kapilar:
- Niski koszt
- Prostota i niezawodność w działaniu, zarówno przy stałym obciążeniu, jak i w warunkach przejściowych.
Natężenie przepływu czynnika chłodniczego przez rurkę kapilarną zależy tylko od różnicy ciśnień na końcach rurki. Jeśli ciśnienie wylotowe sprężarki i obciążenie parownika nie są stałe, wówczas przepływ czynnika chłodniczego przez rurkę kapilarną może stać się niewystarczający lub, przeciwnie, nadmierny.
Jeśli obciążenie cieplne parownika spadnie, ciekły czynnik chłodniczy nie zmieni się całkowicie w parę i może uszkodzić sprężarkę, jeśli do niego wejdzie. Nazywa się to młotem wodnym.
Jeśli z powodu spadku temperatury otoczenia ciśnienie skraplania maleje, przepływ czynnika chłodniczego zmniejsza się, a skraplacz staje się niewystarczający. Jednocześnie zmniejszy się wydajność chłodnicza instalacji, co oczywiście jest niepożądane.
Termostatyczny zawór rozprężny
Do wydajnych instalacji klimatyzacyjnych użyj zaworu termostatycznego (TRV). Reguluje przepływ czynnika chłodniczego ze skraplacza do parownika, dzięki czemu przy zmianie warunków pracy ciśnienie parowania i przegrzanie w parowniku agregatu pozostają niezmienne.Istnieją dwa rodzaje zaworów termostatycznych:
1. Z wyrównaniem wewnętrznym - dla maszyn małej i średniej mocy2. Z wyrównaniem zewnętrznym - dla maszyn dużej mocy
Natężenie przepływu czynnika chłodniczego przez zawór termostatyczny zależy od położenia zaworu. To położenie jest określone przez stosunek sił działających na membranę regulatora.
- Ciśnienie parowania i siła naciągu sprężyny są skierowane na zamknięcie zaworu.
- Ciśnienie w zaworze jest kierowane do otworu zaworu, który jest określony przez przegrzanie czynnika chłodniczego w parowniku.
Podobnie działanie regulatora wraz ze wzrostem temperatury zewnętrznej.
W zależności od długości i sztywności sprężyny zamykającej zawór zaworu termostatycznego ciśnienie parowania i przegrzanie można ustawić na żądane wartości
Strona 2
Temperatury ujemne w danym zakresie mogą być zapewnione przez jednostkę freonową o przybliżonej wydajności chłodniczej około 4000 kcal / hw punkcie wrzenia, freonie - 35 ° C i temperaturze kondensacji freonu - - 30 ° C.
Ciśnienie krytyczne freonów jest 4–8 razy, ciepło parowania około 13 razy, przewodność cieplna i napięcie powierzchniowe są 7 razy, pojemność cieplna i lepkość kinematyczna są 5 razy mniejsze niż wody. Powoduje to szereg cech procesów wymiany ciepła podczas gotowania i kondensacji freonów w porównaniu z wodą dobrze zbadaną w tym sensie.
Zmiany sprawności cieplnej układów wodno-freonowych przy początkowych parametrach cyklu freonu (Rof 15 - 10 Pa. F 120 C w zależności od temperatury kondensacji freonu. |
Przy równych parametrach początkowych i końcowych nowe elektrownie wodne mają wydajność cieplną niższą niż podstawowe elektrownie parowe. Aby osiągnąć taką samą rentowność przy równych początkowych parametrach pary, temperatura kondensacji freonu powinna być niższa niż temperatura kondensacji pary w turbinach K-1200-240 w temperaturze 16-20 ° C, w turbinach K-800-240 w temperaturze 17 ° C, w turbinach nasyconych pary w temperaturze 8-12 C.
Temperatura otoczenia jest jednym z głównych czynników wpływających na działanie lodówki. Wraz ze wzrostem temperatury powietrza pogarszają się warunki chłodzenia skraplacza, co prowadzi do wzrostu ciśnienia skraplania freonu, aw konsekwencji do zmniejszenia wydajności chłodniczej sprężarki. W tym samym czasie zwiększa się napływ zewnętrznego ciepła do lodówki, wzrasta ciśnienie i temperatura wrzenia freonu w parowniku. Wszystko to wpływa na chłodzenie parownika i lodówki. Agregat chłodniczy pracuje z dużym współczynnikiem czasu pracy, zwiększa się zużycie energii przez silnik i wzrasta zużycie energii.
Możliwość kondensacji freonu w separatorze oleju zwiększa się, gdy w skraplaczu znajduje się powietrze, co często zdarza się, gdy maszyny niskotemperaturowe pracują z próżnią po stronie ssącej. Jeśli w skraplaczu znajduje się powietrze, ciśnienie cząstkowe freonu w separatorze oleju jest wyższe niż w skraplaczu, dlatego kondensacja freonu w separatorze oleju występuje w wyższej temperaturze i jest możliwa przy stosunkowo ciepłej wodzie.
W kondensatorach freonowych stosuje się rurki czerwono-miedziane, na zewnętrznej powierzchni których walcowane są żebra spiralne. Konieczność użebrowania powierzchni skraplaczy freonowych po stronie czynnika chłodniczego wynika z faktu, że współczynniki przenikania ciepła są znacznie niższe podczas kondensacji freonów niż woda chłodząca. Zastosowanie rur miedzianych tłumaczy się czystością powierzchni, brakiem korozji, łatwością walcowania żeber i mniejszymi stratami ciśnienia wody. Ale jednocześnie zwiększa się koszt skraplacza, wzrasta korozja blach stalowych na styku z rurami miedzianymi, szczególnie gdy są chłodzone wodą morską. Aby nadać arkuszowi rurowemu pełną odporność na korozję na wodę morską, na kręconą stalową powierzchnię nakłada się warstwę miedzi o znacznej grubości.
W autonomicznych klimatyzatorach zastosowano kondensatory dwururowe, które są dwiema rurami włożonymi do siebie i zagiętymi w cewkę. Czasami zewnętrzna rura jest zastępowana gumowym wężem. W takim przypadku kondensacja freonu zachodzi w rurze wewnętrznej. Wewnątrz spiralnej cewki w takim skraplaczu znajduje się hermetyczna sprężarka, która przyczynia się do zwartego rozmieszczenia wszystkich urządzeń.
W przypadku stosowania materiałów o wysokiej przewodności cieplnej zjawisko to ma również miejsce, ale wartości oporu cieplnego i różnicy temperatur w ścianie są niewielkie, ich wzrost nie wpływa znacząco na całkowity opór cieplny wody chłodzącej parą. W rezultacie czynnik lokalizacji strumieni ciepła nie wpływa znacząco na ogólną wydajność płytkich rur mosiężnych lub miedzianych, gdy skrapla się na nich para wodna. Jednak w przypadku kondensacji freonów, gdzie współczynnik przenikania ciepła po stronie pary jest stosunkowo niewielki (patrz), rury ze ściankami ze stali nierdzewnej będą dość skuteczne, ponieważ w tym przypadku część oporu cieplnego ściany w całkowitym oporze cieplnym jest niewielka.
Większość freonów używanych jako materiały pędne znajduje się w stanie gazowym w normalnych warunkach (760 mm Hg i 20 ° C), z wyjątkiem freonów 11 i 113, wrzących w temperaturze powyżej 20 ° C. W produkcji opakowań aerozolowych freony stosuje się w stanie skroplonym . W temperaturze otoczenia niewielki wzrost ciśnienia prowadzi do kondensacji freonów gazowych w cieczy.
Kondensacja freonu w separatorze oleju jest możliwa nie tylko podczas pracy, ale także po zatrzymaniu maszyny, gdy temperatura otoczenia jest niższa niż temperatura kondensacji przed zatrzymaniem maszyny. Aby zapobiec dostawaniu się ciekłego freonu do skrzyni korbowej, gdy sprężarka jest zatrzymana, konieczne jest zamknięcie zaworu na przewodzie w celu przeniesienia oleju z separatora oleju do skrzyni korbowej. Podczas uruchamiania sprężarki zawór ten należy otworzyć po rozgrzaniu się separatora oleju i wyparowaniu z niego ciekłego freonu. Aby zmniejszyć kondensację freonu w separatorze oleju po zatrzymaniu sprężarki, wykonaj następujące czynności. Konieczność zamknięcia zaworów komplikuje automatyzację maszyny. Jeśli w skrzyni korbowej sprężarki nagrzewa się olej, dostanie się niewielkiej ilości ciekłego freonu do skrzyni korbowej nie jest niebezpieczne, dlatego przewód obejściowy od separatora oleju do skrzyni korbowej może pozostać otwarty.
Jest to jeden z najważniejszych punktów w działaniu każdego klimatyzatora. Sugerujemy zapoznanie się z głównymi punktami dotyczącymi temperatury kondensacji freonu. Duże obciążenie całej konstrukcji klimatyzatora znajduje się dokładnie w skraplaczu, ponieważ odpowiada za chłodzenie powietrza. Ta funkcja przede wszystkim zapobiega możliwości przechłodzenia systemu.
Kondensacja wody na wymienniku ciepła nigdy się nie rozpocznie, dopóki nie zostanie osiągnięta temperatura kondensacji freonu. Wpływ na to ma przede wszystkim ciśnienie pompowane przez sprężarkę samego klimatyzatora. Aby zrozumieć, kiedy rozpoczyna się proces wymiany ciepła, należy zwrócić uwagę na moment, w którym ciśnienie osiągnie krytyczny moment w skraplaczu. Gdy tylko zostanie to osiągnięte, wówczas gaz freonu wrze w górę (temperatura kondensacji freonu osiąga swój poziom), a freon przekształca się w stan ciekły.
Funkcja
Główną funkcją skraplacza: zmieniając ciśnienie, zmień temperaturę freonu na temperaturę skraplania. Jeśli rozważamy przypadek klimatyzatora w trybie ogrzewania, potrzebny jest wrzący freon. W przypadku chłodzenia konieczna jest konwersja freonu ze stanu ciekłego do gazowego.
W celu odparowania (przejścia) do stanu gazowego freon pochłania ciepło powietrza, a tym samym je ochładza. Jednocześnie pomieszczenie jest opróżniane, ponieważ kondensat tworzy się na wymienniku ciepła, który jest odprowadzany przez rury odwadniające w postaci wody.
Po jednym cyklu konwersji freonu proces powtarza się i gdy tylko temperatura kondensacji freonu zostanie osiągnięta, ponownie chłodzi pomieszczenie i cieszysz się chłodem.
Najnowsze recenzje
Oasis Comfort CL-9
Angelica
27.06.2016
Kupiliśmy Oasis w zeszłym roku. Kuchnia o powierzchni 20 m2 ma przegrodę, dlatego radzono nam wziąć 9-ku. Teraz sam klimatyzator: 1. Plusy Najważniejszym plusem jest cena. Ma cały standardowy zestaw funkcji i filtrów (gdy nie jest zbyt duszno, przełączam go w tryb wentylacji i to wystarczy). Ogrzewanie naprawdę działa (nie wiem, jak to jest ekonomiczne, musiałem włączyć go kilka razy w zimie). Plastik jest wystarczająco tani, ale wygląda na akceptowalny. 2. Wady Naprawdę nie lubiłem pilota, chociaż często go nie używam. Głośno
... Oasis Comfort CL-7
Irina Bludova
19.05.2016
Praca urządzenia w trybach innych niż optymalne (na przykład w warunkach podwyższonej temperatury otoczenia) wpływa na wydajność i bezpieczeństwo agregatu chłodniczego.
W artykule omówiono odchylenia od optymalnego trybu pracy instalacji, opisano warunki ich identyfikacji i eliminacji.
Materiał ten jest w większym stopniu odpowiedzią na pytania redaktorów, w szczególności: „ Ile wydajności chłodzenia mojej instalacji spada w takim cieple i co powinienem zrobić?".
Artykuł będzie przydatny dla specjalistów zajmujących się eksploatacją przemysłowych urządzeń chłodniczych.
Główne wskaźniki działania agregatu chłodniczego - wydajność chłodnicza, zużycie energii, jednostkowe zużycie energii, zużycie wody - zależą od warunek temperaturowy praca agregatu chłodniczego.
Najczęstsze odchylenia, które wpływają na wydajność i bezpieczeństwo agregatu chłodniczego to:
podwyższona temperatura kondensacji pary w skraplaczu;
podwyższona lub zbyt wysoka temperatura pary po stronie tłocznej sprężarki.
Niska temperatura wrzenia *.
Działanie urządzenia chłodniczego w niskiej temperaturze wrzenia, oprócz konsekwencji wskazanych powyżej, może powodować zamarzanie chłodziwa w parowniku, zamrażanie chłodzonych towarów znajdujących się w pobliżu urządzeń chłodzących, wzrost skurczu produktów, a także pogorszenie smarowania sprężarek freonowych.
Temperatura wrzenia jest parametrem samoregulującym. Jego wartość zależy od napływu ciepła do parownika, wydajności chłodniczej sprężarek, prędkości wymiany ciepła w parowniku i wymaganej temperatury chłodzonego obiektu.
Obniżenie temperatury wrzenia następuje, gdy przy zmniejszeniu obciążenia cieplnego wydajność sprężarek uwzględnionych w operacji jest większa niż wydajność urządzeń chłodzących. W takim przypadku konieczne jest wyłączenie niektórych sprężarek. Podczas pracy sprężarek o regulowanej wydajności konieczne jest włączenie automatycznego systemu kontroli wydajności chłodzenia i monitorowanie przydatności technicznej jego działania.
Obniżenie temperatury wrzenia spowodowane pogorszeniem intensywności wymiany ciepła w parowniku jest spowodowane wieloma przyczynami.
Jeśli w układzie brakuje czynnika chłodniczego, parownik nie jest całkowicie wypełniony, a część jego powierzchni wymiany ciepła nie jest używana. Głównymi objawami niewystarczającej ilości czynnika chłodniczego są jego niski poziom w odbiorniku liniowym (lub skraplaczu), a także okresowe rozmrażanie zaworu regulacyjnego wraz ze wzrostem stopnia otwarcia. W takim przypadku system należy uzupełnić czynnikiem chłodniczym. Niewystarczająca ilość czynnika chłodniczego w układzie parowania może wynikać z niewłaściwej regulacji jego zasilania. W takim przypadku konieczne jest zapewnienie wymaganego napełnienia układu parowania poprzez większe otwarcie zaworu regulacyjnego lub odpowiednie dostosowanie urządzeń automatyki.
Płaszcz śnieżny osadzony na zewnętrznej powierzchni urządzeń chłodzących, a także smarowanie ich wewnętrznej powierzchni, znacznie pogarsza przenoszenie ciepła i prowadzi do niższej temperatury wrzenia. Okresowe rozmrażanie urządzeń chłodzących pozwala nie tylko uwolnić je od płaszcza śnieżnego, ale także uwolnić nagromadzony olej. Przyczyną znacznego pogorszenia wymiany ciepła w chłodnicach może być zmniejszenie prędkości krążącego powietrza lub całkowite zaprzestanie jego cyrkulacji z powodu zarastania chłodnicy lub kanałów powietrznych płaszczem śnieżnym, złej konstrukcji układu cyrkulacji powietrza, nieprawidłowo działających wentylatorów lub ich silników elektrycznych.
W przypadku zalanych parowników amoniaku (płaszczowo-rurowe, parowniki panelowe, baterie kolektorowe itp.) Temperatura wrzenia może się zmniejszyć, jeśli w ich dolnej części zgromadzi się duża ilość oleju, co, zajmując część aparatu, zmniejsza aktywną powierzchnię wymiany ciepła.
W urządzeniach do chłodzenia płynu chłodzącego o niewystarczającym stężeniu na rurach parownika skorupa lodowa marznie, co ze względu na odporność termiczną powoduje obniżenie temperatury wrzenia. Zmniejszenie krążenia chłodziwa z powodu znacznego zatkania rurociągów, filtrów, awarii pomp, mieszaczy lub ich silników elektrycznych również obniża temperaturę wrzenia.
Podwyższona temperatura kondensacji **.
Zwiększona temperatura skraplania prowadzi do zmniejszenia wydajności chłodniczej instalacji, wzrostu zużycia energii oraz zmniejszenia technicznych i ekonomicznych wskaźników jej działania.
Temperatura skraplania jest parametrem samoregulującym. Wartość temperatury skraplania, przy której następuje samookreślenie, zależy od wydajności włączonych sprężarek, właściwości wymiany ciepła skraplacza i średniej temperatury czynnika chłodzącego. Obniżenie podwyższonej temperatury kondensacji można przeprowadzić metodami opisanymi powyżej. W niektórych przypadkach, aby obniżyć temperaturę skraplania w agregacie chłodniczym z skraplaczami powietrza przy wysokich temperaturach powietrza, zaleca się spryskiwanie wodą.
Zwiększona temperatura kondensacji podczas odwrotnego zaopatrzenia w wodę może być spowodowana niezadowalającą pracą urządzenia chłodzącego wodę (wieżę chłodniczą). Środki mające na celu poprawę jego wydajności sprowadzają się do zwiększenia dopływu wody obiegowej i poprawy jej dystrybucji, a także do zwiększenia ilości powietrza przepływającego przez wieżę chłodniczą.
Wzrost ciśnienia kondensacji może być spowodowany pogorszeniem wymiany ciepła w kondensatorach w wyniku:
wykluczenia z aktywnego przekazywania ciepła części powierzchni skraplaczy z powodu ich przepełnienia ciekłym czynnikiem chłodniczym (niewystarczająca pojemność odbiorników liniowych, przepełnienie układu lub niskie zasilanie układu odparowywania);
obecność nieskraplających się zanieczyszczeń w skraplaczu (produkty rozkładu powietrza i oleju);
zmniejszenie powierzchni kondensatorów z powodu niewłaściwej naprawy nieszczelnych rur (zaślepianie ich zamiast zastępowania ich nowymi);
pogorszenie wymiany ciepła z powodu zanieczyszczenia powierzchni rur kamieniem wodnym, sedymentacji mułu, alg;
pogorszenie dystrybucji wody chłodzącej z powodu zanieczyszczenia dysz i dystrybutorów w skraplaczach pionowych, nawadniających i wyparnych.
W automatycznych agregatach chłodniczych podwyższone ciśnienie kondensacji może być spowodowane wadami w działaniu regulatorów wody.
Podwyższona temperatura pary po jej sprężeniu w sprężarce.
Przekroczenie faktycznej temperatury wtryskiwanej pary w stosunku do jej wartości optymalnych może wynikać ze zwiększonego przegrzania *** pochłoniętej pary, nadmiernego obniżenia temperatury wrzenia, złego działania chłodzenia i wadliwego działania sprężarki oraz obecności gazów niekondensujących się w układzie. Zwiększone przegrzanie pary na ssaniu zależy od niedostatecznego dopływu czynnika chłodniczego do układu, dużej długości rurociągów ssących i niskiej jakości ich izolacji termicznej.
Najczęstsze usterki sprężarki powodujące podwyższoną temperaturę tłoczenia to:
znaczne zużycie cylindra sprężarki, powodujące duży przepływ pary przez pierścienie tłokowe, a także wycieki zaworów wylotowych lub ssących;
niewystarczające dostarczanie wody do płaszcza chłodzącego sprężarki lub osadzanie się kamienia wodnego na jego ścianach, utrudniając przenoszenie ciepła przez ściany płaszcza;
naruszenie smarowania powierzchni cylindra i ogrzewanie go z powodu zwiększonego tarcia pierścieni tłokowych o jego ściany.
W sprężarkach z dużą ilością smaru obiegowego (śrubowego i obrotowego) temperatura pary po jej sprężeniu zależy nie tyle od temperatury pochłoniętej pary, ale od temperatury i ilości wtryskiwanego oleju.
Wilgotne działanie sprężarki.
Praca sprężarki na mokro występuje, gdy sprężona jest mokra para wodna. Jest to jedna z najbardziej niebezpiecznych nieprawidłowości w działaniu agregatów chłodniczych.
Temperatura ciekłego czynnika chłodniczego podczas sprężania nie rośnie, dlatego występuje silne chłodzenie ściśliwej mieszaniny, a także cylindrów i całej grupy ruchów sprężarki.
Pierwszą oznaką mokrej sprężarki jest gwałtowny spadek temperatury pod koniec sprężania. Silne chłodzenie sprężarki może spowodować zamarznięcie wody w płaszczu chłodzącym i pęknięcie bloku cylindrów. Zwiększenie lepkości oleju i zmniejszenie odstępów prowadzi do intensywnego zużycia sprężarki. Nagłe ochłodzenie cylindra od temperatur około 130-150 ° C do -20 ÷ -30 ° C (gdy część ciekłego czynnika chłodniczego wchodzi do nagrzanej sprężarki) może powodować tak zwany udar cieplny, w wyniku którego wnęka sprężarki ulega zniszczeniu w obecności pęknięć w metalu. Jeśli ilość ciekłego czynnika chłodniczego przekroczy martwą przestrzeń sprężarki, istnieje niebezpieczeństwo uderzenia wodnego. Zawory wylotowe sprężarki tłokowej wykazują znaczny opór dla przepływu ciekłego czynnika chłodniczego, co prowadzi do nadmiernego wzrostu ciśnienia w cylindrze sprężarki i wystąpienia sił niszczących na mechanizmie korbowym korbowodu. Względna objętość martwa sprężarek tłokowych wynosi około 2-4%. Zmiana geometryczna objętości sprężarek śrubowych i rotacyjnych mieści się w przedziale 2,6-5,0. Dlatego do czasu, gdy wnęka wylotowa sprężarki jest podłączona do okna wydechowego, objętość tej wnęki wynosi około 20-40% oryginału. Ponadto w przypadku sprężarek śrubowych i obrotowych sekcja okien wylotowych ma większą powierzchnię niż sekcja zaworów tłocznych sprężarek tłokowych. Dlatego są mniej wrażliwe na mokre bieganie.
Oznaki mokrej pracy sprężarki:
brak przegrzania pary ssącej;
obniżenie temperatury wtryskiwanej pary;
zmiana dźwięku pracującej sprężarki: głośne stukanie zaworów gaśnie i pojawiają się stuknięcia w cylindrze;
zamrażanie cylindrów sprężarki i skrzyni korbowej.
Główne przyczyny dostania się mokrej pary do sprężarki:
nadmierne dostarczanie ciekłego czynnika chłodniczego do układu parowania;
gotowanie się cieczy w zalanych parownikach z gwałtownym spadkiem ciśnienia lub gwałtownym wzrostem obciążenia cieplnego;
kondensacja pary w rurze ssącej podczas długotrwałego postoju lub niskiej temperatury powietrza i słaba izolacja rury.
Obecność worków w rurociągach ssących zwiększa ryzyko, gdy gromadzi się w nich ciekły czynnik chłodniczy i olej, duża część cieczy może dostać się do sprężarki, co prowadzi do uderzenia hydraulicznego.
W przypadku wystąpienia pracy na mokro należy natychmiast zamknąć zawór ssący sprężarki i zatrzymać przepływ ciekłego czynnika chłodniczego do układu parowania. Otwórz zawór ssący, aby nie doszło do uderzeń w sprężarce. Jeśli do sprężarki dostała się znaczna ilość ciekłego czynnika chłodniczego, a sprężarka jest bardzo zimna, w niektórych przypadkach wskazane jest otwarcie obejścia łączącego przewody ssące i tłoczne. W takim przypadku para o wyższej temperaturze wpłynie do cylindrów niż z rury ssącej, a sprężarka może zostać uruchomiona szybciej. W takim przypadku surowo zabrania się zamykania zaworu spustowego.
Zdjęcie 1. Fragment wariantu wyglądu freonowego przemysłowego urządzenia chłodniczego
na sprężarce śrubowej „Bitzer” (Niemcy): (wydajność chłodnicza Q 0 \u003d 229 kW w temperaturze wrzenia t 0 \u003d +5 ° С i temperaturze kondensacji t к \u003d 45 ° С)* Temperatura wrzenia Temperatura wrzenia t 0 jest określana za pomocą manometru próżniowego podłączonego do rury ssącej sprężarki. Wraz ze spadkiem temperatury wrzenia zmniejsza się wydajność chłodzenia instalacji. Moc pobierana przez sprężarkę i zależnie od temperatury wrzenia może albo wzrosnąć, albo zmniejszyć. W warunkach typowych dla urządzeń chłodniczych (t 0 ≤ 10 ° С, t к\u003e 25 ° С) moc maleje wraz ze spadkiem temperatury wrzenia i wzrasta w urządzeniach klimatyzacyjnych. Maksymalne moce odpowiadają w przybliżeniu P k / p 0 \u003d 3.
Zmiana temperatury wrzenia średnio o 1 ° C prowadzi do zmiany wydajności chłodzenia sprężarki o 4-5%, zmiany zużycia energii o 2% i zmiany jednostkowego zużycia energii o 2-3%.
Wysokość temperatury, tj. Różnica między temperaturą powietrza w chłodzonym obiekcie a temperaturą wrzenia lub chłodziwa, przyjmuje się w zakresie 7-10 ° C. Jednak w niektórych przypadkach zarówno 5 ° С (komory owocowe), jak i 12-20 ° С (instalacje okrętowe i domowe) są ekonomicznie uzasadnione. W przypadku parowników, w których ciecze są schładzane, różnica między średnią temperaturą chłodzonej cieczy a temperaturą wrzenia wynosi 4-6 ° C. Najbardziej opłacalne z ekonomicznego punktu widzenia jest głowica temperaturowa dla parowników amoniaku 3-4 ° C, dla freonu 4-5 ° C.
** Temperatura skraplania Temperatura skraplania tk jest określana przez skalę temperatury manometru, który mierzy ciśnienie w skraplaczu.
Wzrost temperatury kondensacji o 1 ° C prowadzi do zmniejszenia wydajności chłodzenia o 1-2%, wzrostu mocy o 1-1,5% i wzrostu jednostkowego zużycia energii o 2-2,5%.
Różnica między temperaturą kondensacji a średnią temperaturą wody jest przyjmowana w granicach 4-6 ° C, co odpowiada temperaturze kondensacji 2-4 ° C, wyższej niż temperatura wody opuszczającej skraplacz. Istnieje tendencja do zmniejszania różnicy temperatur; w płaszczu amoniakalnym i rurowych skraplaczach tę różnicę należy przyjąć równą od 2 do 3 ° C.
Ogrzewanie powietrza w skraplaczach powietrza przyjmuje się na poziomie 5-6 ° C, a różnica temperatur w zakresie od 6 do 9 ° C. Niższa wartość tej różnicy odpowiada wyższemu kosztowi energii elektrycznej i odwrotnie.
*** W freonowych agregatach chłodniczych wyposażonych w wymienniki ciepła, przegrzanie pary po stronie ssącej jest w zakresie od 10 do 45 ° C. W przypadku niskotemperaturowych agregatów chłodniczych wyposażonych w kilka wymienników ciepła to przegrzanie może być znacznie wyższe. Przegrzanie pary czynnika chłodniczego w parowniku jest w większości przypadków niepożądane, jednak w parownikach z zaworami rozprężnymi (w małych agregatach chłodniczych) ustawia się minimalne przegrzanie wymagane dla zaworów rozprężnych (3-4 ° C).
Literatura
1. Działanie lodówek. Bykov A.V. Wydawnictwo „Przemysł spożywczy”, 1977
niska temperatura wrzenia czynnika chłodniczego w układzie odparowywania;
O „pływającym” ciśnieniu kondensacji.
Przy projektowaniu instalacji sprężarki parowej ważna jest kwestia regulacji ciśnienie skraplania. Aby zwiększyć efektywność energetyczną układów chłodniczych, stopniową regulację za pomocą przełączników ciśnieniowych zastępuje się płynną regulacją za pomocą przetwornic częstotliwości (IF). Jest to możliwe w przypadku temperatur kondensacji powyżej 20 0 C (wszystkie obliczenia dotyczą R404A), ponieważ ta temperatura jest minimalną dopuszczalną dla większości sprężarek. Ale długoterminowa praca na granicy zastosowania jest niedopuszczalna, dlatego w obliczeniach wykorzystamy wartość 25 0 С.
Konieczność utrzymania minimum ciśnienie skraplania w niskich temperaturach otoczenia (w celu przezwyciężenia oporu hydraulicznego układu) prowadzi do obowiązkowego stosowania w rosyjskim środowisku naturalnym „zimowego zestawu regulacyjnego” ciśnienie skraplanianp. KVR + NRD lub ICS Danfoss, wraz z falownikiem.
Istnieją dwie metody ciągłego kontrolowania ciśnienia skraplania za pomocą falownika:
- Ze stałą wartością zadaną (jeden czujnik jest używany na linii wysokiego ciśnienia);
- Z ruchomą wartością zadaną (jeden czujnik na linii wysokiego ciśnienia, drugi mierzy temperaturę otoczenia).
Główną różnicą między tymi metodami jest to, że w pierwszym przypadku monitorowana jest ustawiona wartość temperatury skraplania, aw drugim przypadku różnica temperatur.
Regulacja ze stałą wartością zadaną, zwykle dostosowaną do obliczonej wartości temperatury kondensacji (na przykład 45 0 C), jest zwykle stosowana w celu zmniejszenia zużycia energii przez wentylatory skraplacza. Ale jednocześnie takie ustawienie temperatury skraplania prowadzi do wzrostu zużycia energii przez sprężarkę z powodu wzrostu różnicy ciśnienia tłoczenia i ssania. Jednocześnie zwiększenie zużycia energii przez sprężarkę z reguły jest czymś więcej niż zmniejszeniem zużycia energii przez wentylatory.
Zmienna wartość zadana rozwiązuje ten problem. ciśnienie skraplaniaw którym falownik dąży do utrzymania określonej różnicy między odczytami czujników temperatury otoczenia (przeliczonych na ciśnienie) a ciśnieniem kondensacji.
Aby porównać skuteczność dwóch opisanych metod, jednostkę obliczono na podstawie kompresora VOSK HGX34e / 380-4S przy użyciu programu PackColculationIIv3.06. Różnicę temperatur dla metody zmiennoprzecinkowej przyjęto w oparciu o zalecenia 15K; dla metody ze stałą wartością zadaną przyjęto wartość wartości zadanej temperatury skraplania 25 0 С. Takie minimalizowanie wartości zadanej pozwala zmniejszyć stopień sprężania w sprężarce, ale prowadzi do przekroczenia energii zużywanej przez wentylatory skraplacza, ponieważ przez większość czasu wentylatory pracują z prędkością znamionową. Jeśli ustawienie zostanie przekroczone, wentylatory skraplacza będą nadal obracać się z częstotliwością znamionową.
Wyniki obliczeń zestawiono w tabeli, z której wynika, że \u200b\u200bsystem z ruchomą wartością zadaną ciśnienia skraplania zużywa 141 kWh (0,5% całkowitej oszczędności energii) w określonych warunkach niż system ze stałą minimalną wartością zadaną. W związku z tym, z punktu widzenia efektywności energetycznej, w tym przypadku wskazane jest zastosowanie metody kontroli ze stałym ustawieniem minimalnym (wartość ustawienia powinna być możliwie minimalna). Wniosek ten można wyjaśnić: wyjaśnimy ten wniosek: przy ustawieniu minimalnym różnica między temperaturą kondensacji a temperaturą powietrza na wlocie do skraplacza zależy od charakterystyki kondensatora, który jest wybierany ze współczynnikiem bezpieczeństwa. Przy zmiennej wartości zadanej tę samą różnicę ustawia się ręcznie, w oparciu o zalecenia, bez uwzględnienia rzeczywistych charakterystyk wybranego kondensatora, co prowadzi do wzrostu ciśnienia kondensacji, większego stopnia sprężania w sprężarce, a ostatecznie do zużycia energii przez system jako całości.
Zmniejszenie wartości zadanej temperatury skraplania na przetwornicy częstotliwości z 45 do 25 0 C (lub niżej, jeśli to możliwe) może osiągnąć znaczne oszczędności energii, które przekraczają oszczędności wynikające z przełączenia na zmienną wartość zadaną ciśnienia skraplania. Przy prawidłowym zaprojektowaniu z układem inwerterowym zastosowanie zmiennej wartości zadanej ciśnienie skraplania niepraktyczne.
Najlepszy materiał do wykończenia samochodu
Zasady twardnienia ciała
Sprężarka „zrób to sam” - przy minimalnych kosztach złomu
Co jest lepsze: zrób to sam lub fabryczny kompresor do malowania samochodu
Przyczyny awarii pompy paliwa