Il chiller è un'unità di refrigerazione costituita da un circuito refrigerante chiuso (compresi compressore / i, condensatore, valvola termostatica, evaporatore, filtro disidratatore, tubi di collegamento e un set di elementi di controllo e controllo) e un circuito dell'acqua (incluse valvole a sfera, evaporatore, serbatoio di stoccaggio e una pompa dell'acqua) collegata a condotte che forniscono il trasporto di acqua dai consumatori e ritorno. L'evaporatore è un elemento comune per entrambi i circuiti. Passando l'evaporatore, l'acqua si raffredda (mentre il compressore è in funzione).
Punto di ebollizione
Il punto di ebollizione di un liquido dipende dalla pressione ambientale. Più bassa è questa pressione, più basso è il punto di ebollizione. Ad esempio, è noto che l'acqua bolle ad una temperatura di 100 ° C. Ma questo accade solo alla normale pressione atmosferica (760 mmHg). Con l'aumentare della pressione, la temperatura di ebollizione aumenterà e con la sua diminuzione (ad esempio in alta montagna), l'acqua bollirà a una temperatura molto inferiore a 100 ° C. In media, quando la pressione cambia di 27 mm Hg. Art. la temperatura di ebollizione cambierà di 1 ° C.
Liquidi diversi bollono a temperature diverse anche alla stessa pressione esterna. Ad esempio, l'azoto liquido bolle a una temperatura vicina a -77 ° C e l'R-22 freon, che viene utilizzato nella tecnologia di refrigerazione, bolle a una temperatura di -40,8 ° C (alla normale pressione atmosferica).
Calore di vaporizzazione
Quando un liquido evapora, il calore viene assorbito dall'ambiente. Quando il vapore si condensa, al contrario viene rilasciato calore. Il calore della vaporizzazione dei liquidi è molto elevato. Ad esempio, l'energia necessaria per evaporare 1 g di acqua ad una temperatura di 100 ° C (539 calorie / g) è molto più dell'energia necessaria per riscaldare quest'acqua da 0 ° C a 100 ° C (100 calorie / g)! Se il freon liquido viene posto in un recipiente aperto (con pressione atmosferica e temperatura ambiente), bolle immediatamente, assorbendo una grande quantità di calore dall'ambiente. Questo fenomeno viene utilizzato nella macchina di refrigerazione. Solo in esso il freon si trasforma in vapore in un compartimento speciale: l'evaporatore. I tubi dell'evaporatore vengono soffiati da un flusso d'aria. Il freon in ebollizione assorbe il calore da questo flusso d'aria, raffreddandolo. Ma in una macchina di refrigerazione, è impossibile evaporare solo il freon, assorbendo il calore. Dopotutto, allora si formerà un gran numero di vapori e sarà necessario fornire sempre più freon liquidi costantemente. Pertanto, nella macchina di refrigerazione, viene eseguito anche il processo inverso di condensazione: la conversione da vapore a liquido. La condensa di qualsiasi liquido genera calore, che quindi entra nell'ambiente. La temperatura di condensazione, come il punto di ebollizione, dipende dalla pressione esterna. A una pressione elevata, può formarsi condensa a temperature molto elevate. Ad esempio, il freon R-22 inizia a condensare a + 55 ° C se è sotto una pressione di 23 atmosfere (circa 17,5 mila mmHg).
Macchina di refrigerazione
Nella macchina di refrigerazione, il freon si condensa in un compartimento speciale: un condensatore. Il calore rilasciato durante la condensazione viene rimosso dal flusso di refrigerante o aria. Poiché la macchina di refrigerazione deve funzionare continuamente, il freon liquido deve fluire costantemente nell'evaporatore e il suo vapore nel condensatore. Questo processo è ciclico, una quantità limitata di freon circola attraverso la macchina di refrigerazione, evaporando e condensando.
Uno dei componenti principali del chiller è un condensatore, che serve a trasferire l'energia termica dal refrigerante all'ambiente. Molto spesso, il calore viene trasferito in acqua o aria. Il calore generato nel condensatore è di circa il 30% superiore alla capacità di refrigerazione del chiller. Ad esempio, se la capacità di raffreddamento di una macchina è di 20 kW, il condensatore genera 25-27 kW di calore.
Il ciclo di raffreddamento a compressione è costituito da quattro elementi principali:
1. compressore
2. evaporatore
3. condensatore
4. regolatore di flusso.
Questi elementi principali sono collegati da condotte in sistema chiusodove circola il refrigerante (di solito freon). Il refrigerante viene fatto circolare nel circuito dal compressore del chiller.
Ciclo di raffreddamento a compressione
All'uscita dell'evaporatore, il refrigerante è vapore a bassa temperatura e bassa pressione. Quindi il compressore assorbe il refrigerante, la pressione sale a circa 20 atm. E la temperatura raggiunge i 70 - 90 ° C. Successivamente, il vapore refrigerante caldo entra nel condensatore, dove viene raffreddato e condensato. Per il raffreddamento, viene utilizzata acqua o aria. All'uscita del condensatore, il refrigerante è un liquido ad alta pressione. All'interno del condensatore, il vapore deve passare completamente allo stato liquido. Per questo, la temperatura del liquido che esce dal condensatore è di alcuni gradi (solitamente 4-6 ° C) inferiore alla temperatura di condensazione a una data pressione. Quindi il refrigerante (avendo in questo momento uno stato liquido di aggregazione ad alta pressione e temperatura) entra nel regolatore di flusso. Qui la pressione scende bruscamente e si verifica l'evaporazione parziale.
Una miscela di vapore e liquido entra nell'ingresso dell'evaporatore. Nell'evaporatore, il liquido deve passare completamente allo stato di vapore. Pertanto, la temperatura del vapore all'uscita dell'evaporatore è leggermente superiore al punto di ebollizione a una data pressione (generalmente 5-8 ° C). Ciò è necessario affinché anche piccole gocce di refrigerante liquido non penetrino nel compressore, altrimenti il \u200b\u200bcompressore potrebbe danneggiarsi. Il vapore surriscaldato che si forma nell'evaporatore lo lascia e il ciclo riprende per primo.
Quindi, una quantità limitata di refrigerante circola costantemente nella macchina di refrigerazione, cambiando lo stato di aggregazione con la variazione periodica di temperatura e pressione.
Ogni ciclo ha due livelli di pressione definiti. Sul lato ad alta pressione, si trovano condensati di refrigerante e un condensatore. Sul lato a bassa pressione è presente un evaporatore e il refrigerante liquido viene convertito in vapore. Il confine tra le aree di alta e bassa pressione passa in due punti: all'uscita del compressore (valvola di scarico) e all'uscita del regolatore di flusso.
Entalpia di refrigerante
Il ciclo di raffreddamento che si svolge nel chiller è convenientemente rappresentato graficamente. Il diagramma mostra il rapporto tra pressione e contenuto di calore (entalpia) del refrigerante. L'entalpia è una funzione di stato il cui incremento in un processo a pressione costante è uguale al calore ricevuto dal sistema.
- Il ramo sinistro della curva corrisponde al fluido saturo
- Il lato destro corrisponde a una coppia satura.
- Nel punto critico, i rami della curva sono collegati e la sostanza può trovarsi sia in stato liquido che gassoso.
- All'interno della curva è presente una zona corrispondente a una miscela di vapore e liquido.
- A sinistra della curva (nella regione dell'entalpia inferiore) si trova un liquido molto freddo.
- A destra della curva (nella regione di maggiore entalpia) si trova il vapore surriscaldato.
Ciclo di raffreddamento teorico
Nel compressore
Il vapore refrigerante saturo freddo entra nel compressore del chiller (punto C1). Durante la compressione, la sua pressione e temperatura aumentano (punto D). L'entalpia aumenta anche di un importo pari alla proiezione della linea C1-D. Nel diagramma, questo è un segmento НС1-НD.
condensazione
Alla fine del ciclo di compressione del refrigerante, il vapore caldo entra nel condensatore. Qui, a temperatura e pressione costanti, si forma condensa e il vapore caldo si trasforma in un liquido caldo. Sebbene la temperatura sia quasi costante, l'entalpia diminuisce durante la transizione di fase e il calore rilasciato viene rimosso dal condensatore. Questo processo viene visualizzato sul diagramma sotto forma di un segmento parallelo all'asse orizzontale (la pressione è costante).
Il processo nel condensatore del chiller avviene in tre fasi: rimozione del surriscaldamento (D-E), condensa (E-A) e raffreddamento del liquido (A-A1). Il diagramma del diagramma D-A1 corrisponde alla variazione dell'entalpia del refrigerante nel condensatore e mostra la quantità di calore rilasciata durante questo processo.
Rimozione del surriscaldamento.
In questo processo, la temperatura del vapore scende alla temperatura di saturazione. Il calore eccessivo viene rimosso, ma non si verifica il cambiamento nello stato di aggregazione. In questa fase, viene rimosso circa il 10-20% del calore.condensazione
In questa fase, lo stato aggregato del refrigerante cambia. La temperatura rimane costante In questa fase, viene rimosso circa il 60 - 80% del calore.Raffreddamento a liquido
In questo processo, il refrigerante liquido viene raffreddato e si ottiene un liquido superrefrigerato. Lo stato di aggregazione non cambia. Il sottoraffreddamento di liquido in questa fase migliora le prestazioni della macchina di refrigerazione. A un livello costante di consumo di energia, l'abbassamento della temperatura di 1 grado aumenta le prestazioni del chiller dell'1%.Regolatore di portata
Il liquido superrefrigerato con i parametri del punto A2 entra nel regolatore del chiller. È un tubo capillare o una valvola di espansione termostatica. Una forte riduzione della pressione si verifica nel regolatore. Immediatamente dopo il regolatore, il refrigerante inizia a bollire. I parametri della risultante miscela di vapore e liquido corrispondono al punto B.Nell'evaporatore
Una miscela di vapore e liquido (punto B) entra nell'evaporatore della macchina di refrigerazione, dove assorbe il calore dall'ambiente e trasferisce completamente al vapore (punto C1). Questo processo si verifica a temperatura costante, ma l'entalpia aumenta. All'uscita dell'evaporatore, il refrigerante vaporizzato si surriscalda leggermente (segmento C1-C2) in modo che le gocce di liquido evaporino completamente. Per fare ciò, è necessario aumentare l'area della superficie di scambio termico dell'evaporatore (del 4-6% per ogni grado di surriscaldamento). Di solito il surriscaldamento è di 5-8 gradi e l'aumento dell'area di trasferimento del calore raggiunge il 20%. Nell'evaporatore del refrigeratore, l'entalpia del refrigerante cambia del valore di HB-HC2 pari alla proiezione della curva di evaporazione sull'asse orizzontale.Ciclo di raffreddamento reale
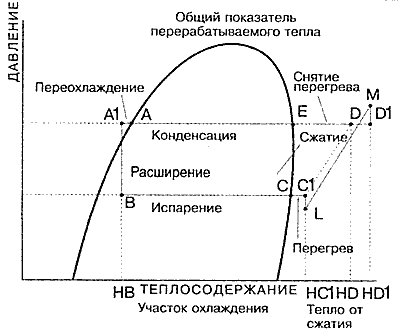
L'attuale ciclo di raffreddamento presenta alcune differenze rispetto all'ideale. Ciò è dovuto alle perdite di carico che si verificano sulle linee di aspirazione e di scarico della macchina di refrigerazione, nonché nelle valvole del compressore. Pertanto, la visualizzazione del ciclo reale sul diagramma della relazione tra pressione ed entalpia è leggermente diversa.
A causa delle perdite di carico all'ingresso del compressore, l'aspirazione deve avvenire a una pressione inferiore alla pressione di evaporazione (segmento C1-L). Inoltre, a causa delle perdite di carico all'uscita, il compressore deve comprimere il vapore del refrigerante a una pressione superiore alla pressione di condensazione (M-D1). Pertanto, il lavoro di compressione è aumentato. Tale compensazione per la perdita di pressione in un chiller reale riduce l'efficienza del ciclo.
Oltre alle perdite di carico nella conduttura, ci sono altre deviazioni dal ciclo ideale. In primo luogo, l'effettiva compressione del refrigerante nel compressore non può essere strettamente adiabatica (senza fornitura e rimozione del calore). Pertanto, il lavoro di compressione è superiore a quello teoricamente calcolato. In secondo luogo, il compressore del chiller presenta perdite di energia meccanica, che portano ad un aumento della potenza del motore elettrico richiesta.
L'efficienza del ciclo di raffreddamento del chiller
Visualizzazione grafico:C1-L - perdita di pressione di aspirazione
M-D1 - perdita di pressione all'uscita
HD-HC1 - variazione teorica dell'entalpia (contenuto di calore) durante la compressione
HD1-HC1 - reale cambiamento di entalpia (contenuto di calore) durante la compressione
C1D - Compressione teorica
LM - compressione reale
Per selezionare il migliore dei cicli di raffreddamento, è necessario valutarne l'efficacia. Tipicamente, l'indicatore di efficienza di un ciclo di una macchina di refrigerazione è l'efficienza o il coefficiente di efficienza termica (termodinamica).
Coefficiente di efficienza termica- questo è: il rapporto tra la variazione di entalpia del refrigerante nell'evaporatore (HC-HB) e la variazione di entalpia durante la compressione (HD-HC).oppure: rapporto tra potenza di raffreddamento e potenza elettrica consumata dal compressore del chiller.
Ad esempio, se il coefficiente di efficienza termica di una macchina frigorifera è 2, quindi per ogni kW di elettricità consumata, questa macchina produce 2 kW di freddo.
Condensatore. Il principio di lavoro.
Condensatori ad aria
![]() 1 tubo di rame 2 alette di raffreddamento |
I condensatori raffreddati ad aria sono i più comuni. Il condensatore raffreddato ad aria è costituito da un'unità di ventilazione con un motore elettrico e uno scambiatore di calore. Il refrigerante scorre attraverso i tubi e una ventola soffia aria attraverso i tubi. In genere, la velocità del flusso è compresa tra 1 e 3,5 m / s. Molto spesso, lo scambiatore di calore è costituito da tubi di rame alettati con un diametro di 6 - 20 mm con una distanza tra le nervature di 1-3 mm. Il rame viene utilizzato perché è facile da lavorare, non si ossida e ha un'alta conduttività termica. Le pinne sono generalmente in alluminio. La scelta del diametro del tubo dipende da molti fattori: perdita di pressione, facilità di lavorazione, ecc. Il tipo di alette può essere diverso e influisce in modo significativo sui parametri termici e idraulici dello scambiatore di calore nel suo insieme. Ad esempio, un profilo complesso di alette con numerose sporgenze e scanalature crea turbolenza (turbolenza) dell'aria che lava lo scambiatore di calore. Di conseguenza, aumenta l'efficienza del trasferimento di calore dal refrigerante all'aria e aumenta la capacità di refrigerazione del chiller. |
Vengono utilizzati due tipi di connessione di tubi con nervature:
I fori nelle nervature in cui i tubi dello scambiatore di calore sono inseriti direttamente. Questo metodo è più semplice, ma riduce il trasferimento di calore a causa di perdite di contatto. Inoltre, la corrosione può apparire in un ambiente contaminato lungo il contorno, riducendo ulteriormente le prestazioni di trasferimento del calore.
Collari (collari) nei punti in cui sono collegati i tubi dello scambiatore di calore. Questo metodo è più costoso e più complicato, ma fornisce un aumento della superficie di trasferimento del calore.
Inoltre, il trasferimento di calore del refrigerante viene aumentato ondulando la superficie interna dei tubi dello scambiatore di calore. Questo crea turbolenza nel flusso del refrigerante.
Tipicamente, un condensatore ha da una a quattro file di tubi situati nella direzione del flusso di refrigerante. Spesso i tubi sono sfalsati per aumentare l'efficienza del trasferimento di calore.
La velocità di trasferimento del calore varia durante il movimento del refrigerante attraverso i tubi. Il refrigerante caldo entra nello scambiatore dall'alto e si sposta verso il basso.
Nella fase iniziale (5% della superficie), il raffreddamento è più intenso, poiché la differenza di temperatura massima tra il refrigerante e l'aria di raffreddamento e l'alta velocità di movimento del refrigerante.
La sezione principale dello scambiatore di calore è circa l'85% della superficie. In questa zona, il refrigerante si condensa a temperatura costante.
Il restante 10% della superficie dello scambiatore di calore serve per un ulteriore raffreddamento del refrigerante liquido.
La temperatura di condensazione del refrigerante (freon) è da 10 a 20 gradi superiore alla temperatura ambiente e di solito è 42-55 ° C. L'aria riscaldata che esce dallo scambiatore di calore è solo 3-5 gradi più fredda della temperatura di condensazione.
Condensatori ad acqua
Esistono tre tipi di design del condensatore raffreddato ad acqua:- Shell e tubo
- Digita "pipe in pipe"
- Plate.
Condensatori a fascio tubiero
Nel processo di scambio termico, non tutta l'aria fornita all'evaporatore è coinvolta, poiché parte di essa passa lungo la periferia oltre lo scambiatore di calore. La percentuale di aria che passa dall'evaporatore e mantiene i suoi parametri è chiamata coefficiente di dispersione. Dovrebbe cercare di ridurre il coefficiente di perdita d'aria.
Un condensatore pipe-in-pipe è un sistema di due tubi a spirale, uno situato all'interno dell'altro. Il refrigerante si muove attraverso uno dei tubi (esterno o interno) e l'acqua si muove lungo l'altro. Il tubo interno è in rame e quello esterno in rame o acciaio. La superficie dei tubi può avere alette, che aumenta l'efficienza del trasferimento di calore. I liquidi si muovono nei flussi in arrivo, con l'acqua che entra dal basso e che scorre dall'alto, e il refrigerante - viceversa. I condensatori da tubo a tubo vengono utilizzati nelle unità di condizionamento autonomo e nelle unità di raffreddamento a bassa potenza. Lo svantaggio di questo tipo di condensatori è che il design è monoblocco e solo la pulizia chimica del tubo è possibile.Condensatori a piastre
I condensatori a piastre sono costituiti da file di piastre in acciaio disposte a "spina di pesce". All'interno dello scambiatore di calore, il refrigerante e l'acqua si spostano l'uno verso l'altro lungo circuiti di circolazione indipendenti.
Pertanto, sono ampiamente utilizzati nei frigoriferi di piccola e media potenza.
Se la temperatura dell'acqua all'ingresso del condensatore è di 16 gradi, la temperatura di condensazione è di 32-36 gradi. A una temperatura dell'acqua di + 24 ° C, il refrigerante si condensa a 38-40 ° C.
La pressione massima consentita nella modalità operativa dal lato del circuito del refrigerante è di 2,45 MPa e dal lato del circuito dell'acqua - 1 MPa.
evaporatore
Uno dei componenti principali del chiller è un evaporatore, che serve a raffreddare l'ambiente di lavoro. Aria, acqua o liquidi contenenti antigelo vengono utilizzati come mezzo di lavoro del refrigeratore. Vari tipi di evaporatori sono progettati per raffreddare diversi tipi di mezzi di lavoro:- Shell e tubo
- grembiule
Evaporatori a fascio tubiero
L'evaporatore a fascio tubiero è un cilindro in acciaio, i reticoli in acciaio sono installati su entrambe le estremità del cilindro, a cui sono montate teste con ugelli per il collegamento a un sistema di raffreddamento ad acqua. Tubi di rame attraverso i quali scorre l'acqua vengono pressati in queste griglie. I tubi sono spesso realizzati in rame e hanno un diametro di 20 mm e 25 mm. All'esterno, sono a costine per migliorare il trasferimento di calore.
Il refrigerante circola attraverso i tubi, proviene dal fondo dell'evaporatore e sale gradualmente attraverso i tubi. All'esterno, i tubi vengono lavati con acqua, che viene raffreddata durante lo scambio di calore con refrigerante freddo.
L'acqua in un evaporatore a fascio tubiero circola perpendicolare ai tubi e ha una velocità da 0,5 a 3 m / s a \u200b\u200bcausa delle pareti divisorie situate all'interno dell'involucro dell'evaporatore.
Gli evaporatori a fascio tubiero sono adatti per la gestione di vari refrigeranti. La potenza di questi evaporatori varia da 7 a 200-250 kW.
Evaporatori a piastre
Gli evaporatori a piastre sono costituiti da file di piastre in acciaio disposte a "spina di pesce". All'interno dello scambiatore di calore, il refrigerante e l'acqua si spostano l'uno verso l'altro lungo circuiti di circolazione indipendenti.vantaggi:
- altissima efficienza di trasferimento del calore.
- compattezza e leggerezza.
- più resistente al congelamento in caso di guasto rispetto ad altri tipi di evaporatori.
Evaporatori per raffreddamento ad aria
Gli evaporatori d'aria sono scambiatori di calore con una o più (4-6) file di tubi. Il refrigerante scorre all'interno dei tubi e l'aria fredda scorre tra le alette dell'evaporatore (fuori dai tubi).
Molto spesso, un evaporatore per l'aria di raffreddamento è costituito da tubi di rame alettati con un diametro di 8-13 mm (5/16 ", 3/8" e 1/2 ") con una distanza tra le alette di 1,4 - 1,8 mm. Il rame viene utilizzato perché è facile da lavorare, non è ossidato e ha un'elevata conduttività termica e il finning è generalmente in alluminio.
Se la capacità del chiller è abbastanza grande, gli evaporatori ad aria sono realizzati con due o più circuiti di raffreddamento. Ogni circuito ha una fornitura indipendente di refrigerante attraverso un distributore collegato ad esso da tubi sottili. Tutti i circuiti sono riempiti con uguali quantità di refrigerante. Il flusso d'aria viene distribuito uniformemente sullo scambiatore di calore, escludendo la formazione di ghiaccio delle singole sezioni dell'evaporatore.
Per ottenere la migliore qualità e stabilità dell'evaporatore del chiller, la potenza dovrebbe essere di 3-7 kW per ciascun circuito di trasferimento del calore (quando si utilizza il refrigerante R-22 più comune).
Le dimensioni dell'evaporatore dipendono dal volume di aria raffreddata. Il volume d'aria è di circa 195 metri cubi / ora per ogni kW di capacità di raffreddamento dell'impianto. La capacità di refrigerazione totale dell'evaporatore è determinata dalla temperatura di evaporazione del refrigerante (costante, impostata durante la progettazione della macchina di refrigerazione) e dalla temperatura dell'aria in ingresso (dipende dalle condizioni operative).
La velocità dell'aria che entra nell'evaporatore è generalmente di 2-3 m / s. Se la velocità è maggiore, le gocce di condensa potrebbero scivolare all'uscita dello scambiatore di calore. Nell'evaporatore, come in altri elementi del refrigeratore, si verificano perdite di pressione. Dipendono dal diametro dei tubi dell'evaporatore, dalla configurazione delle alette, dalla velocità dell'aria e dalla quantità di condensa sulle alette.
Tasso di perdita (bypass)
Vantaggi della bassa percentuale di perdite:
- Aumenta la temperatura di evaporazione e le prestazioni del refrigeratore
- È possibile ridurre le dimensioni del compressore
- È possibile limitarsi a una superficie più piccola dello scambiatore di calore. Necessari meno tubi scambiatori di calore.
compressore
Uno degli elementi principali di qualsiasi refrigeratore è un compressore.
Il compressore assorbe il vapore di refrigerante a bassa temperatura e pressione, quindi lo comprime, aumentando la temperatura (fino a 70 - 90 ° C) e la pressione (fino a 15 - 25 atm.), Quindi indirizza il refrigerante vaporizzato al condensatore.
Le caratteristiche principali del compressore sono il grado di compressione (compressione) e la quantità di refrigerante che può pompare. Il rapporto di compressione è il rapporto tra la massima pressione di uscita del vapore del refrigerante e la massima entrata.
I frigoriferi utilizzano due tipi di compressori:
pistone - con pistoni alternativi nei cilindri
Rotativo, a vite e a spirale - con movimento rotatorio delle parti di lavoro
1. Compressori a pistoni
2. Compressori rotativi a rotazione
3. Compressori scroll SCROLL
4. Avvitare i compressori
Compressori a pistoni
Quando il pistone (3) si sposta verso l'alto sul cilindro del compressore (4), il refrigerante viene compresso. Il pistone viene mosso da un motore elettrico attraverso l'albero motore (6) e la biella (5).
Sotto l'influenza della pressione del vapore, le valvole di aspirazione e di scarico del compressore del chiller si aprono e si chiudono.
La Figura 1 mostra la fase di assorbimento del refrigerante nel compressore. Il pistone inizia a cadere dal punto superiore, mentre viene creato un vuoto nella camera del compressore e la valvola di ingresso (12) si apre. Il refrigerante di vapore a bassa temperatura e bassa pressione entra nello spazio di lavoro del compressore.
La Figura 2 mostra la fase di compressione del vapore e la sua uscita dal compressore. Il pistone si alza e comprime il vapore. Allo stesso tempo, la valvola di uscita del compressore (1) si apre e il vapore ad alta pressione esce dal compressore.
Le principali modifiche dei compressori alternativi (si differenziano per design, tipo di motore e scopo):
- Compressori ermetici
- Compressori semiermetici
- Compressori aperti
Compressori ermetici
Utilizzato in refrigeratori di bassa potenza (1,5 - 35 kW). Il motore elettrico si trova all'interno dell'alloggiamento del compressore sigillato. Il motore è raffreddato dal refrigerante di aspirazione stesso.Compressori semiermetici
Utilizzato in refrigeratori di medie dimensioni (30 - 300 kW). Nei compressori semiermetici, il motore elettrico e il compressore sono collegati direttamente e collocati in un contenitore pieghevole. Il vantaggio di questo tipo di compressore è che in caso di danni, il motore può essere rimosso per riparare valvole, pistone e altre parti del compressore. Il motore è raffreddato dal refrigerante di aspirazione stesso.Compressori aperti
Hanno un motore elettrico esterno, prelevato all'esterno dell'alloggiamento e collegato direttamente al compressore o tramite una trasmissione. La potenza di molte unità di refrigerazione può essere regolata continuamente con l'aiuto di inverter: dispositivi speciali che modificano la velocità di rotazione del compressore. Nei compressori semiermetici, è anche possibile un altro modo di regolare la potenza: bypassare il vapore dall'uscita all'entrata o chiudendo la parte delle valvole di aspirazione.I principali svantaggi dei compressori alternativi:
Increspature della pressione del vapore del refrigerante all'uscita, con conseguenti livelli di rumore elevati.Elevati carichi di avviamento, che richiedono una grande riserva di potenza e portano all'usura del compressore.
Compressori rotativi rotanti
Il principio di funzionamento dei compressori rotativi a rotazione si basa sull'assorbimento e la compressione del gas durante la rotazione delle piastre.Il loro vantaggio rispetto ai compressori alternativi è rappresentato dalle pulsazioni a bassa pressione e dalla diminuzione della corrente all'avvio.
Esistono due modifiche ai compressori rotativi:
- Con piastre fisse
- Con piastre rotanti
Compressore a piastre fisse
In un compressore con piastre fisse, il refrigerante viene compresso mediante un eccentrico montato sul rotore del motore. Quando il rotore ruota, l'eccentrico rotola lungo la superficie interna del cilindro del compressore e il vapore di refrigerante davanti a esso viene compresso e quindi spinto fuori attraverso la valvola di uscita del compressore. Le piastre separano le aree di alta e bassa pressione del vapore di refrigerante all'interno del cilindro del compressore.
La compressione e l'aspirazione continuano
La compressione è completata, il vapore ha infine riempito lo spazio all'interno del cilindro del compressore.
Compressore a tavola rotante
Steam riempie lo spazio disponibile
Inizia la compressione del vapore all'interno del compressore e l'assorbimento di una nuova porzione di refrigerante
La compressione e l'aspirazione sono completate.
Inizia un nuovo ciclo di aspirazione e compressione.
Compressori scroll SCROLL
I compressori Scroll sono utilizzati in frigoriferi di piccola e media potenza.
Tale compressore è costituito da due spirali d'acciaio. Sono inseriti l'uno nell'altro e si espandono dal centro verso il bordo del cilindro del compressore. La spirale interna è fissata in modo fisso e quella esterna ruota attorno ad essa.
Le spirali hanno un profilo speciale (a spirale) che consente loro di rotolare senza scivolare. Il rotolo del compressore è montato su un eccentrico e rotola lungo la superficie interna di un altro rotolo. In questo caso, il punto di contatto delle spirali si sposta gradualmente dal bordo al centro. Il vapore di refrigerante davanti alla linea tattile viene compresso e spinto nel foro centrale nel coperchio del compressore. I punti di contatto si trovano su ogni giro della spirale interna, quindi le coppie vengono compresse più uniformemente, in porzioni più piccole rispetto ad altri tipi di compressori. Di conseguenza, il carico sul motore del compressore si riduce, soprattutto al momento dell'avvio del compressore.
Il vapore di refrigerante entra attraverso l'ingresso nella parte cilindrica dell'alloggiamento, raffredda il motore, quindi viene compresso tra le spirali ed esce attraverso l'uscita nella parte superiore dell'alloggiamento del compressore.
Svantaggi dei compressori scroll:
- La complessità della produzione.
- È necessario un adattamento molto preciso delle spirali e una tenuta alle estremità.
I compressori a vite sono utilizzati in refrigeratori di alta potenza (150 - 3500 kW). Esistono due modifiche di questo tipo:
- Vite singola
- Doppia vite
Compressore a vite singola
I modelli a vite singola hanno uno o due ingranaggi satellite collegati lateralmente al rotore.
Il vapore del refrigerante viene compresso usando i rotori che ruotano in direzioni opposte. La loro rotazione fornisce un rotore centrale sotto forma di una vite. Il vapore di refrigerante entra attraverso l'ingresso del compressore, raffredda il motore, quindi entra nel settore esterno degli ingranaggi rotanti dei rotori, viene compresso ed esce attraverso una valvola scorrevole nell'uscita.
Le viti del compressore devono essere ben serrate, pertanto viene utilizzato olio lubrificante. Successivamente, l'olio viene separato dal refrigerante in uno speciale separatore del compressore.
Compressore a doppia vite
I modelli a doppia vite si distinguono per l'uso di due rotori: il principale e il convertitore.
I compressori a vite non hanno valvole di entrata e di uscita. Il refrigerante viene costantemente aspirato da un lato del compressore e lo scarico dall'altro lato. Con questo metodo di compressione del vapore, il livello di rumore è molto più basso di quello dei compressori alternativi.
I compressori a vite consentono di regolare uniformemente la potenza del chiller modificando la velocità del motore.
Regolatore di portata
1. Tubo capillare2. Valvola di espansione termostatica
Tubo capillare
Il refrigerante liquido che fluisce dal condensatore all'evaporatore deve essere dosato. Questo è implementato usando un regolatore di flusso.
La versione più semplice del regolatore è un tubo capillare con un diametro di circa 1 mm. Sono utilizzati nei condizionatori d'aria di sistemi split di bassa potenza.
Vantaggi dei tubi capillari:
- Basso costo
- Semplicità e affidabilità nel funzionamento, sia a carico costante che in condizioni transitorie.
La portata del refrigerante attraverso il tubo capillare dipende solo dalla pressione differenziale alle estremità del tubo. Se la pressione di scarico del compressore e il carico dell'evaporatore non sono costanti, il flusso di refrigerante attraverso il tubo capillare potrebbe diventare insufficiente o, al contrario, eccessivo.
Se il carico di calore sull'evaporatore diminuisce, il refrigerante liquido non si trasforma completamente in vapore e può danneggiarlo se entra. Questo si chiama colpo d'ariete.
Se, a causa di una diminuzione della temperatura ambiente, la pressione di condensazione diminuisce, il flusso di refrigerante diminuirà e il condensatore diventerà insufficiente. Allo stesso tempo, la capacità di raffreddamento dell'installazione diminuirà, il che, ovviamente, è indesiderabile.
Valvola di espansione termostatica
Per impianti di condizionamento potenti utilizzare una valvola termostatica (TRV). Regola il flusso di refrigerante dal condensatore all'evaporatore in modo che, quando cambiano le condizioni operative, la pressione di evaporazione e il surriscaldamento nell'evaporatore del chiller rimangono costanti.Esistono due tipi di valvole termostatiche:
1. Con equalizzazione interna - per macchine a bassa e media potenza2. Con equalizzazione esterna - per macchine ad alta potenza
La portata del refrigerante attraverso la valvola termostatica dipende dalla posizione della valvola. Questa posizione è determinata dal rapporto delle forze che agiscono sulla membrana del regolatore.
- La pressione di evaporazione e la forza di tensione della molla sono dirette alla chiusura della valvola.
- La pressione della valvola è diretta verso l'apertura della valvola, che è determinata dal surriscaldamento del refrigerante nell'evaporatore.
Allo stesso modo, l'azione del regolatore con l'aumento della temperatura esterna.
A seconda della lunghezza e della rigidità della molla che chiude la valvola della valvola termostatica, la pressione di evaporazione e il surriscaldamento possono essere impostati sui valori desiderati
Pagina 2
Temperature negative in un determinato intervallo possono essere fornite da un'unità freon con una capacità di raffreddamento approssimativa di circa 4000 kcal / h in un punto di ebollizione, freon - 35 C e una temperatura di condensazione di freon - - 30 C.
Le pressioni critiche dei freoni sono 4–8 volte, il calore della vaporizzazione è di circa 13 volte, la conduttività termica e la tensione superficiale sono 7 volte, la capacità termica e la viscosità cinematica sono 5 volte inferiori a quelle dell'acqua. Ciò provoca una serie di caratteristiche dei processi di trasferimento del calore durante l'ebollizione e la condensazione dei freoni rispetto all'acqua ben studiata in questo senso.
Cambiamenti nell'efficienza termica delle unità acqua-freon ai parametri iniziali del ciclo di freon (Rof 15 - 10 Pa. F 120 C a seconda della temperatura di condensazione del freon. |
Con uguali parametri iniziali e finali, gli impianti acqua-freo-nuovi hanno un'efficienza termica inferiore rispetto agli impianti base a turbina a vapore. Per ottenere la stessa efficienza con uguali parametri iniziali del vapore, la temperatura di condensazione del freon deve essere inferiore alla temperatura di condensazione del vapore per le turbine K-1200-240 a 16-20 C, per le turbine K-800-240 a 17 C, per le turbine a vapore saturo a 8-12 S.
La temperatura ambiente è uno dei principali fattori che influenzano il funzionamento del frigorifero. Con l'aumentare della temperatura dell'aria, le condizioni di raffreddamento del condensatore peggiorano, il che porta ad un aumento della pressione di condensazione del freon e, di conseguenza, a una diminuzione della capacità di refrigerazione del compressore. Allo stesso tempo, aumenta l'afflusso di calore esterno nel frigorifero, aumentano la pressione e la temperatura di ebollizione del freon nell'evaporatore. Tutto ciò influisce sul raffreddamento dell'evaporatore e del frigorifero. L'unità di refrigerazione funziona con un elevato coefficiente di tempo di lavoro, aumenta il consumo di energia del motore e aumenta il consumo di energia.
La possibilità di condensazione del freon nel separatore d'olio aumenta quando c'è aria nel condensatore, cosa che spesso accade quando le macchine a bassa temperatura funzionano con il vuoto sul lato di aspirazione. Se è presente aria nel condensatore, la pressione parziale del freon nel separatore dell'olio è superiore rispetto al condensatore, pertanto la condensazione del freon nel separatore dell'olio si verifica a una temperatura più elevata ed è possibile con acqua relativamente calda.
Nei condensatori freon, vengono utilizzati tubi di rame rosso, sulla superficie esterna di cui vengono arrotolate le nervature a spirale. La necessità di nervature della superficie dei condensatori freon sul lato del refrigerante è dovuta al fatto che i coefficienti di trasferimento del calore sono molto più bassi durante la condensazione dei freon rispetto all'acqua di raffreddamento. L'uso di tubi di rame è spiegato dalla pulizia della superficie, dall'assenza di corrosione, dalla facilità di rotolamento delle nervature e dalle minori perdite di pressione dell'acqua. Ma allo stesso tempo, aumenta il costo del condensatore, aumenta la corrosione dei fogli di tubi di acciaio alla giunzione con i tubi di rame, specialmente se raffreddati dall'acqua di mare. Per dare alla lastra del tubo una completa resistenza alla corrosione contro l'acqua di mare, uno strato di rame di notevole spessore viene applicato sulla superficie dell'acciaio riccio.
Nei condizionatori d'aria autonomi sono stati utilizzati condensatori a due tubi, che sono due tubi inseriti l'uno nell'altro e piegati in una bobina. A volte il tubo esterno viene sostituito con un tubo di gomma. In questo caso, la condensa del freon si verifica nella camera d'aria. All'interno della bobina a spirale in un tale condensatore è presente un compressore ermetico, che contribuisce alla disposizione compatta di tutte le apparecchiature.
Nel caso dell'uso di materiali altamente conduttori di calore, si verifica anche questo fenomeno, ma i valori di resistenza termica e differenza di temperatura nella parete sono piccoli, il loro aumento non influisce in modo significativo sulla resistenza termica totale dell'acqua di raffreddamento a vapore. Di conseguenza, il fattore di localizzazione dei flussi di calore non influisce in modo significativo sull'efficienza complessiva dei tubi poco profondi in ottone o rame quando il vapore acqueo è condensato su di essi. Tuttavia, nel caso della condensazione dei freoni, in cui il coefficiente di trasferimento del calore sul lato vapore è relativamente piccolo (vedi), i tubi in acciaio inossidabile con pareti poco profonde saranno abbastanza efficaci, poiché in questo caso la frazione della resistenza termica della parete nella resistenza termica totale è piccola.
La maggior parte dei freon usati come propellenti sono allo stato gassoso in condizioni normali (760 mm Hg e 20 C), ad eccezione dei freon 11 e 113, con ebollizione superiore a 20 C. Nella produzione di pacchetti di aerosol, i freon sono utilizzati in uno stato liquefatto . A temperatura ambiente, un leggero aumento della pressione porta alla condensazione di freoni gassosi in un liquido.
La condensa del freon nel separatore d'olio è possibile non solo durante il funzionamento, ma anche quando la macchina è ferma, quando la temperatura ambiente è inferiore alla temperatura di condensazione prima di arrestare la macchina. Per evitare che il freon liquido entri nel basamento quando il compressore è fermo, è necessario chiudere la valvola sulla linea per trasferire l'olio dal separatore d'olio al basamento. All'avvio del compressore, questa valvola deve essere aperta dopo il riscaldamento del separatore d'olio e l'evaporazione del liquido libero da esso. Segue la riduzione della condensa del freon nel separatore d'olio dopo l'arresto. La necessità di chiudere le valvole complica l'automazione della macchina. In caso di riscaldamento dell'olio nel basamento del compressore, ottenere una piccola quantità di freon liquido nel basamento non è pericoloso, pertanto la linea di bypass dal separatore dell'olio al basamento potrebbe rimanere aperta.
Questo è uno dei punti più importanti nel funzionamento di qualsiasi condizionatore d'aria. Ti consigliamo di familiarizzare con i punti principali che riguardano la temperatura di condensazione del freon. Un grande carico sull'intero design del condizionatore d'aria si trova esattamente nel condensatore, perché è responsabile del raffreddamento dell'aria. Questa funzione impedisce principalmente la possibilità di raffreddare eccessivamente il sistema.
La condensa dell'acqua sullo scambiatore di calore non inizierà mai fino al raggiungimento della temperatura di condensazione del freon. Ciò è principalmente influenzato dalla pressione pompata dal compressore del condizionatore d'aria stesso. Per capire quando inizia il processo di trasferimento del calore, è necessario prestare attenzione a quando la pressione raggiunge il momento critico nel condensatore. Non appena viene raggiunto, il gas freon bolle (la temperatura di condensazione del freon raggiunge il suo livello) e il freon viene convertito in uno stato liquido.
funzione
La funzione principale del condensatore: cambiando la pressione, cambia la temperatura del freon alla sua temperatura di condensazione. Se stiamo considerando il caso del condizionatore d'aria in modalità riscaldamento, è necessario un freon in ebollizione. Se si raffredda, è necessario convertire il freon dallo stato liquido a quello gassoso.
Per la sua evaporazione (transizione) in uno stato gassoso, il freon assorbe il calore dell'aria e quindi lo raffredda. Allo stesso tempo, la tua stanza viene drenata, poiché si forma condensa sullo scambiatore di calore, che viene scaricato attraverso tubi di drenaggio sotto forma di acqua.
Dopo un ciclo di conversione del freon, il processo si ripete e non appena viene raggiunta la temperatura di condensazione del freon, raffredda nuovamente la stanza e ti godi il fresco.
Ultime recensioni
Oasis Comfort CL-9
angelica
27.06.2016
Abbiamo comprato un Oasis l'anno scorso. La cucina di 20 m2 ha una partizione, quindi ci hanno consigliato di prendere un 9-ku. Ora per il condizionatore d'aria stesso: 1. Pro Il vantaggio più importante è il prezzo. Ha l'intero set standard di funzioni e filtri (quando non è troppo soffocante, lo metto in modalità ventilazione e questo è sufficiente). Il riscaldamento funziona davvero (non so quanto sia economico, ho dovuto accenderlo più volte durante l'inverno). La plastica è abbastanza economica ma sembra accettabile. 2. Contro non mi piaceva molto il telecomando, anche se spesso non lo uso. Rumoroso.
... Oasis Comfort CL-7
Irina Bludova
19.05.2016
Il funzionamento dell'apparecchiatura in modalità diverse da quella ottimale (ad esempio, in condizioni di temperature ambiente elevate) influisce sull'efficienza e sulla sicurezza dell'unità di refrigerazione.
L'articolo discute le deviazioni dalla modalità operativa ottimale dell'installazione, descrive le condizioni per la loro identificazione ed eliminazione.
Questo materiale è in gran parte la risposta alle domande ricevute dagli editori, in particolare: " Quanto diminuisce la capacità di raffreddamento della mia installazione in tale calore e cosa devo fare?".
L'articolo sarà utile agli specialisti impegnati nel funzionamento di apparecchiature di refrigerazione industriale.
I principali indicatori del funzionamento dell'unità di refrigerazione - capacità di raffreddamento, consumo di energia, consumo specifico di energia, consumo di acqua - dipendono da condizione di temperatura unità di refrigerazione di lavoro.
Le deviazioni più comuni che incidono sull'efficienza e sulla sicurezza dell'unità di refrigerazione sono:
aumento della temperatura di condensazione del vapore nel condensatore;
temperatura del vapore aumentata o eccessivamente alta sul lato di scarico del compressore.
Punto di ebollizione basso *.
Il funzionamento dell'unità di refrigerazione in un punto di ebollizione basso, oltre alle conseguenze sopra indicate, può causare il congelamento del refrigerante nell'evaporatore, il congelamento di prodotti refrigerati situati vicino a dispositivi di raffreddamento, un aumento del restringimento dei prodotti e anche un deterioramento della lubrificazione dei compressori freon.
Il punto di ebollizione è un parametro autoregolante. Il suo valore è determinato dall'afflusso di calore all'evaporatore, dalla capacità di raffreddamento dei compressori, dalla velocità di trasferimento del calore nell'evaporatore e dalla temperatura richiesta dell'oggetto raffreddato.
L'abbassamento del punto di ebollizione si verifica quando, quando il carico termico viene ridotto, le prestazioni dei compressori inclusi nell'operazione sono superiori a quelle dei dispositivi di raffreddamento. In questo caso, è necessario spegnere alcuni compressori. Quando si utilizzano compressori con capacità regolabile, è necessario attivare il sistema di controllo automatico della capacità di raffreddamento e monitorare la funzionalità del suo funzionamento.
L'abbassamento del punto di ebollizione causato dal deterioramento dell'intensità del trasferimento di calore nell'evaporatore è dovuto a molte ragioni.
In caso di mancanza di refrigerante nel sistema, l'evaporatore non viene riempito completamente e non viene utilizzata parte della sua superficie di trasferimento del calore. I principali segni di insufficiente refrigerante sono il suo basso livello nel ricevitore lineare (o condensatore), nonché lo scongelamento periodico della valvola di controllo con un aumento del suo grado di apertura. In questo caso, il sistema deve essere riempito con refrigerante. Una quantità insufficiente di refrigerante nel sistema di evaporazione può derivare da una regolazione errata della sua fornitura. In questo caso, è necessario garantire il riempimento richiesto del sistema di evaporazione aprendo la valvola di controllo più grande o regolando i dispositivi di automazione di conseguenza.
Lo strato di neve depositato sulla superficie esterna dei dispositivi di raffreddamento, nonché l'ingrassaggio della loro superficie interna, compromette significativamente il trasferimento di calore e porta ad un punto di ebollizione più basso. Lo scongelamento periodico dei dispositivi di raffreddamento consente non solo di liberarli dal manto nevoso, ma anche di rilasciare l'olio accumulato. La causa di un significativo deterioramento dello scambio di calore dei dispositivi di raffreddamento dell'aria può essere una diminuzione della velocità dell'aria in circolazione o una completa cessazione della sua circolazione a causa del sovraffollamento del dispositivo di raffreddamento dell'aria o dei condotti dell'aria con uno strato di neve, cattivo design del sistema di circolazione dell'aria, malfunzionamento dei ventilatori o dei loro motori elettrici.
Con gli evaporatori di ammoniaca allagati (guscio e tubo, evaporatori a pannello, batterie del collettore, ecc.), Il punto di ebollizione può diminuire se si accumula una grande quantità di olio nella parte inferiore che, occupando parte dell'apparato, riduce la superficie di trasferimento di calore attiva.
Nei dispositivi per il raffreddamento del liquido di raffreddamento con una concentrazione insufficiente sui tubi dell'evaporatore, la crosta di ghiaccio si congela, il che, essendo resistenza termica, provoca un abbassamento del punto di ebollizione. Ridurre la circolazione del refrigerante a causa di un significativo intasamento di tubazioni, filtri, guasti delle pompe, miscelatori o dei loro motori elettrici riduce anche il punto di ebollizione.
Aumento della temperatura di condensazione **.
L'aumento della temperatura di condensazione comporta una diminuzione della capacità di raffreddamento dell'impianto, un aumento del consumo di energia e una diminuzione degli indicatori tecnici ed economici del suo funzionamento.
La temperatura di condensazione è un parametro autoregolante. Il valore della temperatura di condensazione alla quale si verifica l'autodeterminazione dipende dalle prestazioni dei compressori accesi, dalle proprietà di trasferimento del calore del condensatore e dalla temperatura media del mezzo di raffreddamento. La riduzione della temperatura di condensazione aumentata può essere effettuata con i metodi sopra descritti. In alcuni casi, per ridurre la temperatura di condensazione in un'unità di refrigerazione con condensatori d'aria ad alte temperature dell'aria, è consigliabile spruzzare acqua.
L'aumento della temperatura di condensa durante l'alimentazione dell'acqua inversa può essere causato dal funzionamento insoddisfacente del dispositivo di raffreddamento ad acqua (torre di raffreddamento). Le misure volte a migliorare le sue prestazioni si riducono ad aumentare la fornitura di acqua circolante e migliorare la sua distribuzione, nonché ad aumentare la quantità di aria che passa attraverso la torre di raffreddamento.
Un aumento della pressione di condensazione può essere causato da un deterioramento del trasferimento di calore nei condensatori a seguito di:
esclusioni dal trasferimento di calore attivo di una parte della superficie dei condensatori a causa del loro riempimento eccessivo con refrigerante liquido (capacità insufficiente dei ricevitori lineari, riempimento eccessivo del sistema o scarsa fornitura al sistema di evaporazione);
la presenza di impurità non condensabili nel condensatore (prodotti di decomposizione dell'aria e dell'olio);
riduzione della superficie dei condensatori dovuta alla riparazione impropria di tubi che perdono (tappandoli invece di sostituirli con nuovi);
deterioramento del trasferimento di calore a causa della contaminazione della superficie dei tubi con calcoli d'acqua, sedimentazione di fanghi, alghe;
deterioramento della distribuzione dell'acqua di raffreddamento a causa della contaminazione di ugelli e distributori nei condensatori verticali, di irrigazione ed evaporazione.
Nelle unità di refrigerazione automatizzate, l'aumento della pressione di condensa può essere causato da difetti nel funzionamento dei regolatori dell'acqua.
Elevata temperatura del vapore dopo che è stata compressa nel compressore.
Il superamento della temperatura effettiva del vapore iniettato rispetto ai suoi valori ottimali può derivare da un aumento del surriscaldamento *** del vapore assorbito, da un eccessivo abbassamento del punto di ebollizione, da uno scarso raffreddamento e da malfunzionamenti del compressore e dalla presenza di gas non condensabili nel sistema. L'aumento del surriscaldamento del vapore all'aspirazione dipende dall'insufficiente fornitura di refrigerante al sistema, dalla grande lunghezza delle tubazioni di aspirazione e dalla scarsa qualità del loro isolamento termico.
I malfunzionamenti del compressore più comuni che causano una temperatura di scarico elevata sono:
usura significativa del cilindro del compressore, causando un grande passaggio di vapore attraverso le fasce elastiche, nonché perdite delle valvole di scarico o di aspirazione;
fornitura insufficiente di acqua alla camicia di raffreddamento del compressore o deposizione di pietra d'acqua sulle sue pareti, compromettendo il trasferimento di calore attraverso le pareti della camicia;
violazione della lubrificazione della superficie del cilindro e riscaldamento a causa di un maggiore attrito degli anelli del pistone contro le sue pareti.
Per i compressori con abbondante lubrificante a circolazione (a vite e rotante), la temperatura del vapore dopo la sua compressione dipende non tanto dalla temperatura del vapore assorbito, ma dalla temperatura e dalla quantità di olio iniettato.
Funzionamento umido del compressore.
Il funzionamento a umido del compressore si verifica quando il vapore umido viene compresso. Questa è una delle anomalie più pericolose nel funzionamento delle unità di refrigerazione.
La temperatura del refrigerante liquido durante la compressione non aumenta, pertanto si verifica un forte raffreddamento della miscela comprimibile, nonché dei cilindri e dell'intero gruppo di movimenti del compressore.
Il primo segno di funzionamento a umido del compressore è una forte diminuzione della temperatura della fine della compressione. Un forte raffreddamento del compressore può causare il congelamento dell'acqua nella camicia di raffreddamento e la rottura del blocco cilindri. L'aumento della viscosità dell'olio e la riduzione degli spazi vuoti comporta un'usura intensiva del compressore. Il raffreddamento improvviso del cilindro da temperature di circa 130-150 ° С a -20 ÷ -30 ° С (quando una parte di refrigerante liquido entra nel compressore preriscaldato) può causare il cosiddetto colpo di calore, a seguito del quale, in presenza di crepe nel metallo, la cavità del compressore viene distrutta. Se la quantità di refrigerante liquido supera lo spazio morto del compressore, sussiste il pericolo di colpo d'ariete. Le valvole di scarico del compressore alternativo presentano una resistenza significativa al flusso di refrigerante liquido, che porta a un eccessivo aumento della pressione nel cilindro del compressore e al verificarsi di forze distruttive sul meccanismo di manovella della biella. Il volume morto relativo dei compressori alternativi è di circa 2-4%. La variazione geometrica del volume della vite a vapore e dei compressori rotanti è nell'intervallo 2.6-5.0. Pertanto, quando la cavità di scarico del compressore è collegata alla finestra di scarico, il volume di questa cavità è circa il 20-40% dell'originale. Inoltre, per i compressori a vite e rotativi, la sezione delle finestre di uscita ha un'area più ampia rispetto alla sezione delle valvole di scarico dei compressori alternativi. Pertanto, sono meno sensibili alla corsa sul bagnato.
Segni di funzionamento a umido del compressore:
nessun surriscaldamento del vapore in aspirazione;
abbassando la temperatura del vapore iniettato;
cambiando il suono di un compressore in funzione: il forte bussare delle valvole diventa sordo e i colpi compaiono nel cilindro;
congelamento dei cilindri del compressore e del basamento.
Le principali cause del vapore umido che entra nel compressore sono:
eccesso di fornitura di refrigerante liquido al sistema di evaporazione;
ebollizione del liquido negli evaporatori allagati con una forte diminuzione della pressione in essi o con un forte aumento del carico termico;
condensazione del vapore nel tubo di aspirazione durante un parcheggio prolungato o bassa temperatura dell'aria e scarso isolamento del tubo.
La presenza di sacchi nelle tubazioni di aspirazione aumenta il rischio, quando si accumulano liquido refrigerante e olio in essi, gran parte del liquido può penetrare nel compressore, provocando un colpo d'ariete.
Se si verifica un funzionamento a umido, chiudere immediatamente la valvola di aspirazione del compressore e arrestare il flusso di refrigerante liquido nel sistema di evaporazione. Aprire la valvola di aspirazione in modo che non vi siano colpi nel compressore. Se una quantità significativa di refrigerante liquido è entrata nel compressore e il compressore è molto freddo, in alcuni casi è consigliabile aprire il bypass che collega le linee di aspirazione e di scarico. In questo caso, il vapore con una temperatura più alta fluirà nei cilindri rispetto al tubo di aspirazione e il compressore può essere messo in funzione più velocemente. In questo caso è severamente vietato chiudere la valvola di scarico.
Foto 1. Un frammento di una variante dell'aspetto di un'unità di refrigerazione industriale freon
su un compressore a vite "Bitzer" (Germania): (capacità di raffreddamento Q 0 \u003d 229 kW in un punto di ebollizione t 0 \u003d +5 ° С e una temperatura di condensazione t к \u003d 45 ° С)* Punto di ebollizione. Il punto di ebollizione t 0 è determinato da un misuratore di vuoto collegato al tubo di aspirazione del compressore. Con una diminuzione del punto di ebollizione, la capacità di raffreddamento dell'installazione diminuisce. La potenza consumata dal compressore e, a seconda del punto di ebollizione, può aumentare o diminuire. Nelle condizioni tipiche delle unità di refrigerazione (t 0 ≤ 10 ° С, t к\u003e 25 ° С), la potenza diminuisce con il diminuire del punto di ebollizione e aumenta le unità di condizionamento dell'aria. I massimi di potenza corrispondono approssimativamente a P k / p 0 \u003d 3.
Una variazione del punto di ebollizione di 1 ° C in media comporta una variazione della capacità di raffreddamento del compressore del 4-5%, una variazione del consumo di energia del 2% e una variazione del consumo di energia specifico del 2-3%.
La prevalenza della temperatura, ovvero la differenza tra la temperatura dell'aria nell'oggetto refrigerato e il punto di ebollizione o il refrigerante, viene rilevata nell'intervallo 7-10 ° C. Tuttavia, in alcuni casi, sia il 5 ° С (camere della frutta) che il 12-20 ° С (navi e installazioni domestiche) sono giustificati economicamente. Per gli evaporatori in cui i liquidi vengono raffreddati, la differenza tra la temperatura media del liquido da raffreddare e il punto di ebollizione viene presa nell'intervallo di 4-6 ° C. Il più possibile da un punto di vista economico è la temperatura nominale per evaporatori di ammoniaca 3-4 ° C, per freon 4-5 ° C.
** Temperatura di condensazione. La temperatura di condensazione tk è determinata dalla scala di temperatura del manometro che misura la pressione nel condensatore.
Un aumento della temperatura di condensazione di 1 ° C comporta una riduzione della capacità di raffreddamento dell'1-2%, un aumento della potenza dell'1,5% e un aumento del consumo specifico di energia del 2-2,5%.
La differenza tra la temperatura di condensazione e la temperatura media dell'acqua viene rilevata entro 4-6 ° C, che corrisponde a una temperatura di condensazione di 2-4 ° C, superiore alla temperatura dell'acqua che esce dal condensatore. Vi è la tendenza a ridurre la differenza di temperatura; nei condensatori a guscio e tubo di ammoniaca, questa differenza dovrebbe essere presa pari a 2 - 3 ° C.
Il riscaldamento dell'aria nei condensatori ad aria è pari a 5-6 ° C e la differenza di temperatura nell'intervallo da 6 a 9 ° C. Un valore inferiore di questa differenza corrisponde a un costo più elevato dell'elettricità e viceversa.
*** Nelle unità di refrigerazione freon dotate di scambiatori di calore, surriscaldamento del vapore sul lato di aspirazione è nell'intervallo da 10 a 45 ° C. Per le unità di refrigerazione a bassa temperatura dotate di più scambiatori di calore, questo surriscaldamento può essere significativamente più elevato. Il surriscaldamento del vapore di refrigerante nell'evaporatore è nella maggior parte dei casi indesiderabile, tuttavia, negli evaporatori con valvole di espansione (in piccoli refrigeratori), viene impostato il surriscaldamento minimo richiesto per le valvole di espansione (3-4 ° C).
letteratura
1. Funzionamento dei frigoriferi. Bykov A.V. Casa editrice "Industria alimentare", 1977
basso punto di ebollizione del refrigerante nel sistema di evaporazione;
Informazioni sulla pressione di condensazione "flottante".
Quando si progetta un'installazione di un compressore a vapore, il problema della regolamentazione è importante pressione di condensazione. Per aumentare l'efficienza energetica dei sistemi di refrigerazione, la regolazione passo-passo mediante pressostati viene sostituita dalla regolazione regolare con l'uso di convertitori di frequenza (IF). Questo è possibile per temperature di condensazione superiori a 20 0 C (tutti i calcoli sono per R404A), poiché questa temperatura è il minimo consentito per la maggior parte dei compressori. Ma il lavoro a lungo termine al limite dell'applicazione è inaccettabile, quindi nei calcoli useremo il valore 25 0 С.
La necessità di mantenere un minimo pressione di condensazione a basse temperature ambiente (per superare la resistenza idraulica del sistema) porta all'uso obbligatorio nell'ambiente naturale della Russia "kit di regolazione invernale" pressione di condensazionead es. KVR + NRD o ICS Danfoss, insieme all'inverter.
Esistono due metodi per controllare continuamente la pressione di condensazione utilizzando un inverter:
- Con un set point fisso (un sensore viene utilizzato sulla linea ad alta pressione);
- Con un set point mobile (un sensore sulla linea di alta pressione, il secondo misura la temperatura ambiente).
La principale differenza tra questi metodi è che nel primo caso viene monitorato il valore impostato della temperatura di condensazione e nel secondo la differenza di temperatura.
La regolazione con un setpoint fisso, generalmente adattata al valore calcolato della temperatura di condensazione (ad esempio, 45 0 C), viene solitamente utilizzata per ridurre il consumo di energia dei ventilatori del condensatore. Allo stesso tempo, una tale impostazione della temperatura di condensazione porta ad un aumento del consumo di energia del compressore a causa di un aumento della differenza nella pressione di scarico e di aspirazione. Allo stesso tempo, aumentare il consumo di energia del compressore, di norma, è più che ridurre il consumo di energia dei ventilatori.
Il setpoint mobile risolve questo problema. pressione di condensazionein cui l'inverter cerca di mantenere una data differenza tra le letture dei sensori di temperatura ambiente (convertiti in pressione) e la pressione di condensazione.
Per confrontare l'efficacia dei due metodi descritti, l'unità è stata calcolata sulla base del compressore VOSK HGX34e / 380-4S utilizzando il programma PackColculationIIv3.06. La differenza di temperatura per il metodo del set point variabile è stata adottata in base alle raccomandazioni, 15K; per il metodo con un setpoint fisso, il valore del setpoint per la temperatura di condensazione è stato preso 25 0 С. Tale riduzione al minimo del setpoint consente di ridurre il grado di compressione nel compressore, ma porta a una spesa eccessiva dell'energia consumata dai ventilatori del condensatore, poiché la maggior parte del tempo i ventilatori funzionano alla velocità nominale. Se l'impostazione viene superata, le ventole del condensatore continuano a ruotare alla frequenza nominale.
I risultati del calcolo sono riepilogati nella tabella, dalla quale segue che un sistema con un set point mobile per la pressione di condensazione consuma 141 kWh (0,5% del risparmio energetico totale) più in condizioni specificate rispetto a un sistema con un set point minimo fisso. Di conseguenza, dal punto di vista dell'efficienza energetica, in questo caso è consigliabile applicare con precisione il metodo di controllo con un'impostazione minima fissa (il valore dell'impostazione dovrebbe essere il minimo possibile). Questa conclusione è spiegabile, spiegheremo questa conclusione: all'impostazione minima, la differenza tra la temperatura di condensazione e la temperatura dell'aria all'ingresso del condensatore è determinata dalle caratteristiche del condensatore, che viene selezionato con un fattore di sicurezza. Con un valore di setpoint variabile, la stessa differenza viene impostata manualmente, in base alle raccomandazioni, senza tener conto delle caratteristiche reali del condensatore selezionato, che porta ad un aumento della pressione di condensazione, a un maggior grado di compressione nel compressore e, in definitiva, al consumo di energia del sistema nel suo insieme.
La riduzione del setpoint della temperatura di condensazione sul convertitore di frequenza da 45 a 25 0 C (o inferiore, se possibile) può consentire significativi risparmi energetici che superano i risparmi derivanti dal passaggio a un setpoint di pressione di condensazione flottante. Se progettato correttamente con un sistema di inverter, l'uso di un setpoint mobile pressione di condensazione inexpedient.
Il miglior materiale per il rivestimento dell'auto
Principi di indurimento del corpo
Compressore fai-da-te - con costi di scarto minimi
Che è meglio: compressore fai-da-te o fatto in fabbrica per dipingere un'auto
Cause di malfunzionamento della pompa del carburante